Fully Automatic Transformer Radiator Fin Production Line
The entire line consists of an automatic decoiler, roll former, turnover platform, multiple spot welders, side seam welding machine, head welding machine, side shearing machine, head cutting machine, and forwarding table, among others.
The available sizes are 320, 460, 480, 520, and 535, or they can be custom-designed based on the client’s specific requirements.
The panel length ranges from 1000mm to 4500mm. The entire line is fully automatic, ensuring high product quality and top-tier performance that meets world-class standards.
- Capacity config: 60 pcs/h (based on 2m products)
- Operators: 1 person
- Equipment area: 65m *6.5m*2m(L*W*H)
- Equipment power distribution: 330KVA
Product Descriptions
Workflow
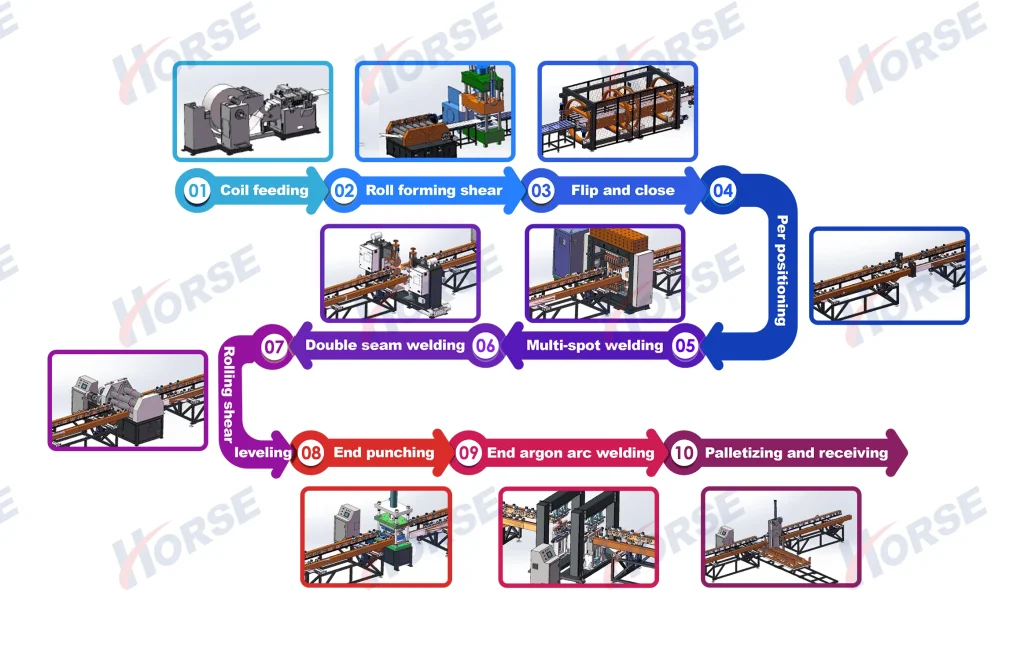
Work flow:Decoiling→roll forming→ hydraulic press→ turn over → multiple spot welding→ side seam welding → head welding → side shearing → head cutting → end product → automatic panel stacking machine
Main equipments
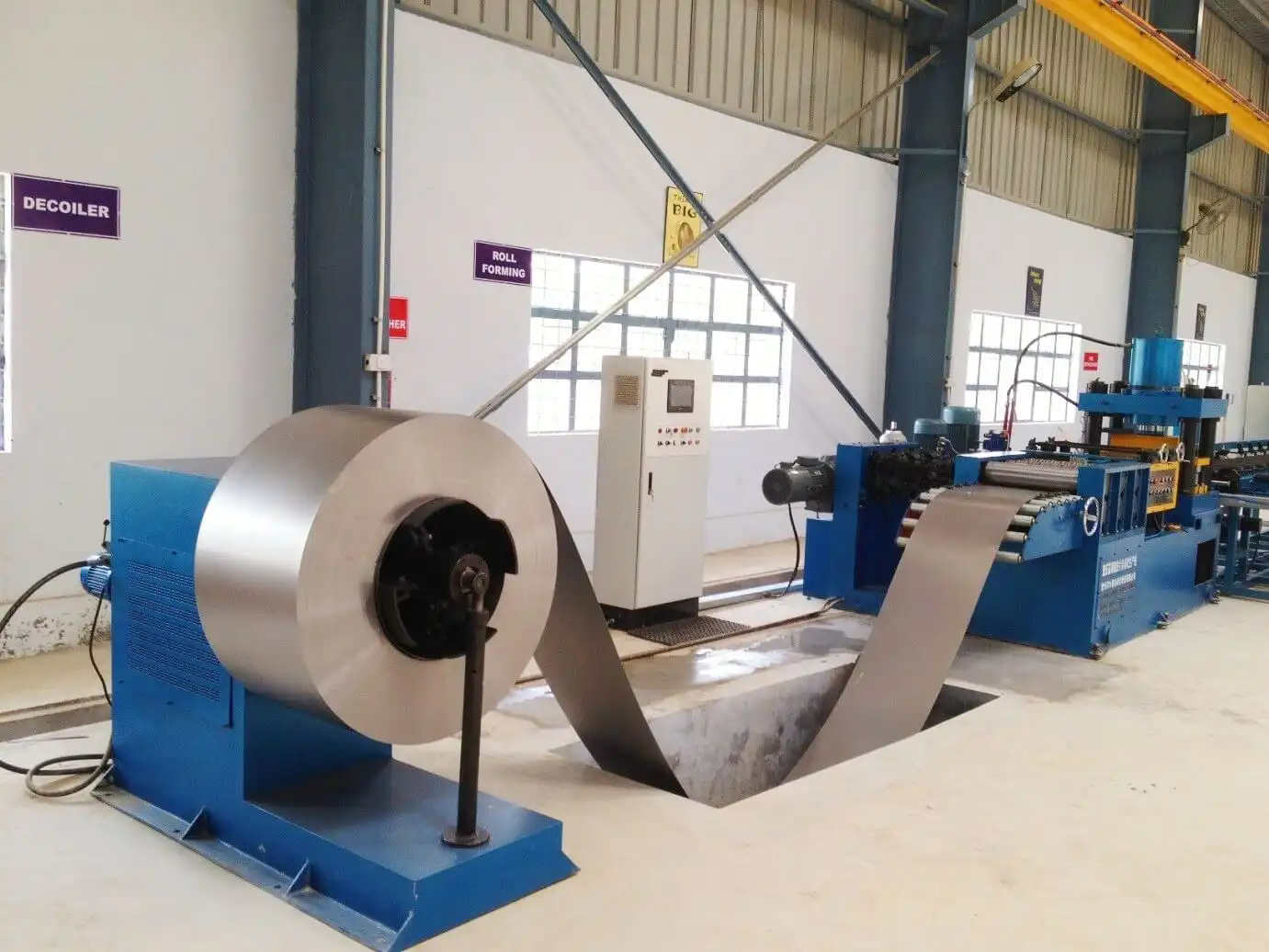
Rolling forming station
Rolling speed: 6-14 m/min
Adjustable pressure
End punch: 315-ton hydraulic press
Rotary encoder & servo drive for length/size accuracy of fins
Leveling mechanism ensures flatness of single piece
Unrolled material placed on 5-ton unloading rack via loading trolley & rolled into sheets
Optional buffer pit per customer request
Flipping and joining station
Conveying speed: 5-15 m/min
180° flipping of radiator fins
Flipping device: rotating rack, flipping rack, transmission system, flipping device, pushing device, etc.
First sheet reaches preset position → flipped to opposite conveying rack
Second sheet reaches preset position → pushing device moves it onto the first sheet, completing the joining
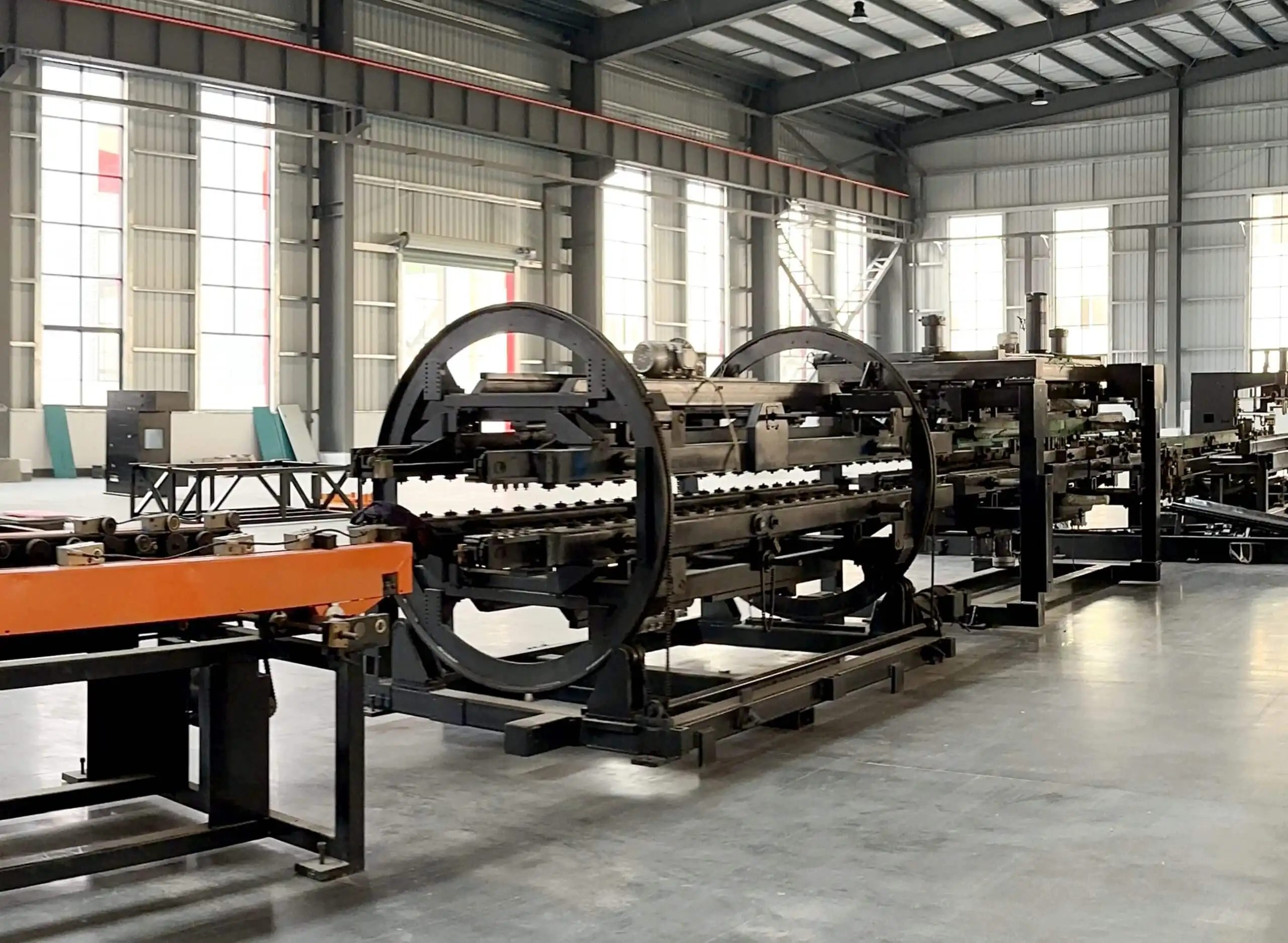
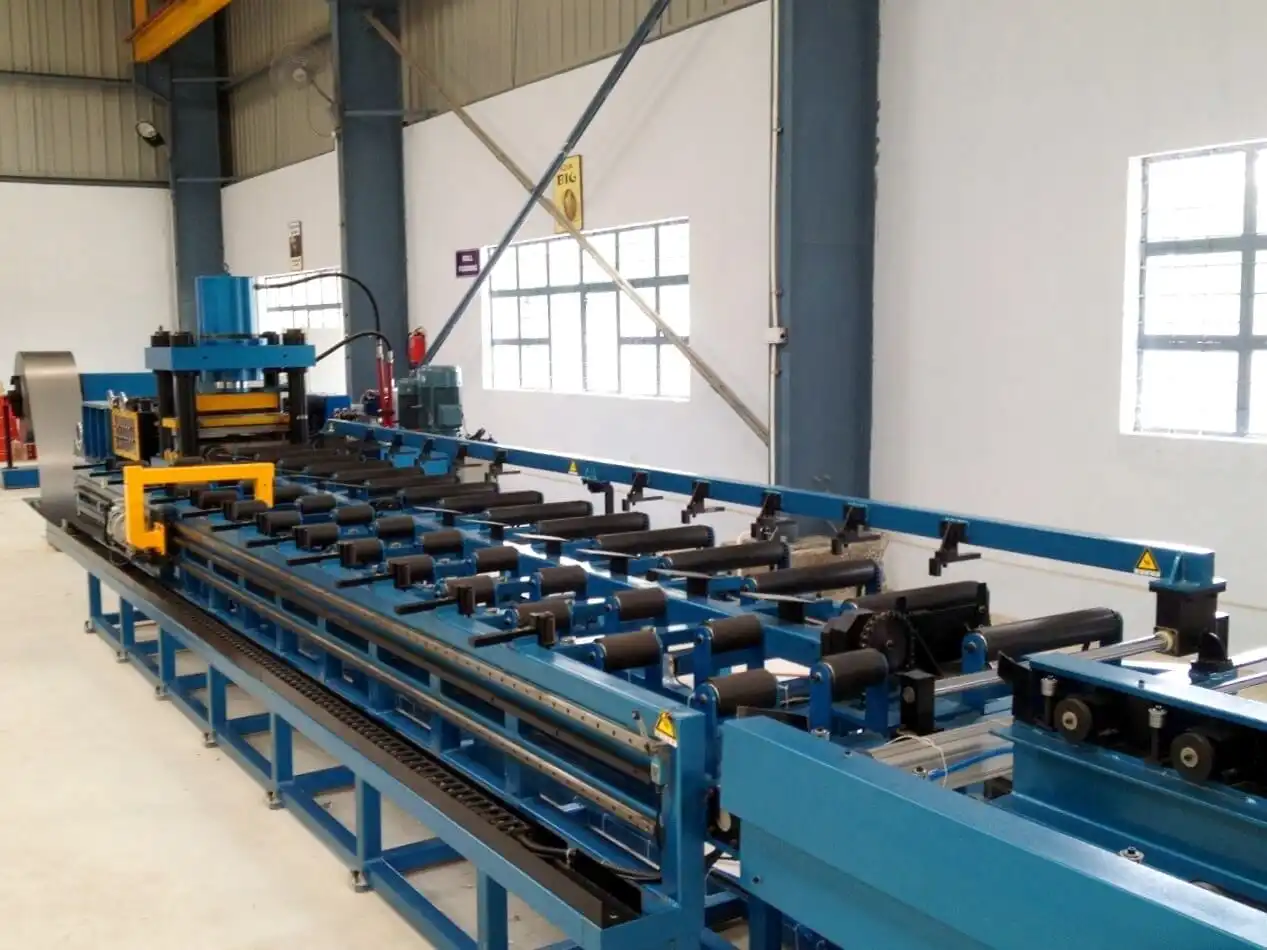
Double-head pre-spot welding station
Two sets of spot welding pressure devices
Power: 60 KVA
After flipping & assembly, pre-spot welding machine aligns & fixes workpieces for multi-spot welding
Gantry multi-spot welding station
12 sets of spot welding pressure devices
Double-head welding head, 6 points/row
AC power supplies: 12 sets
Power: 12 * 50 KVA
Double-row welding for improved efficiency
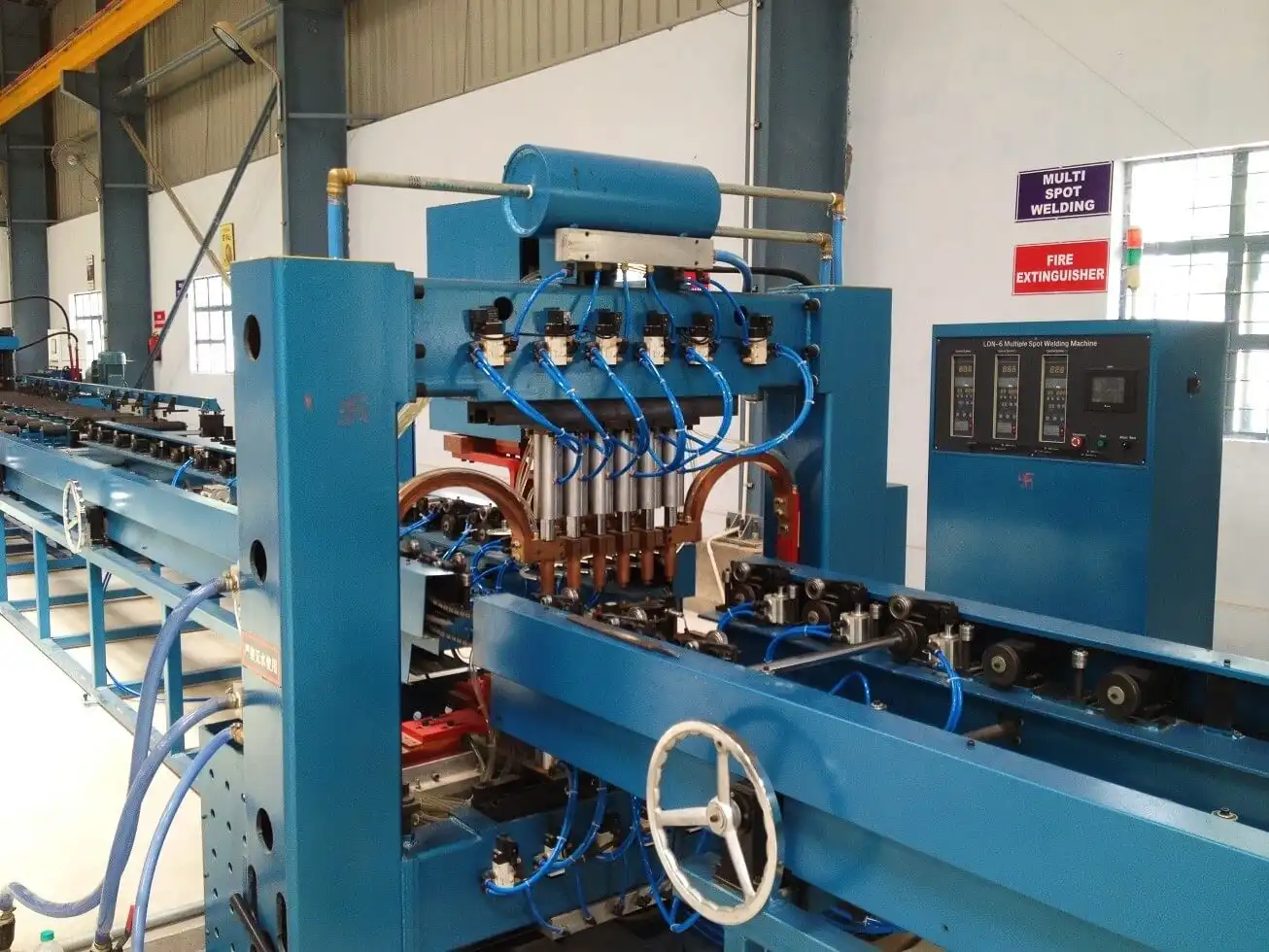
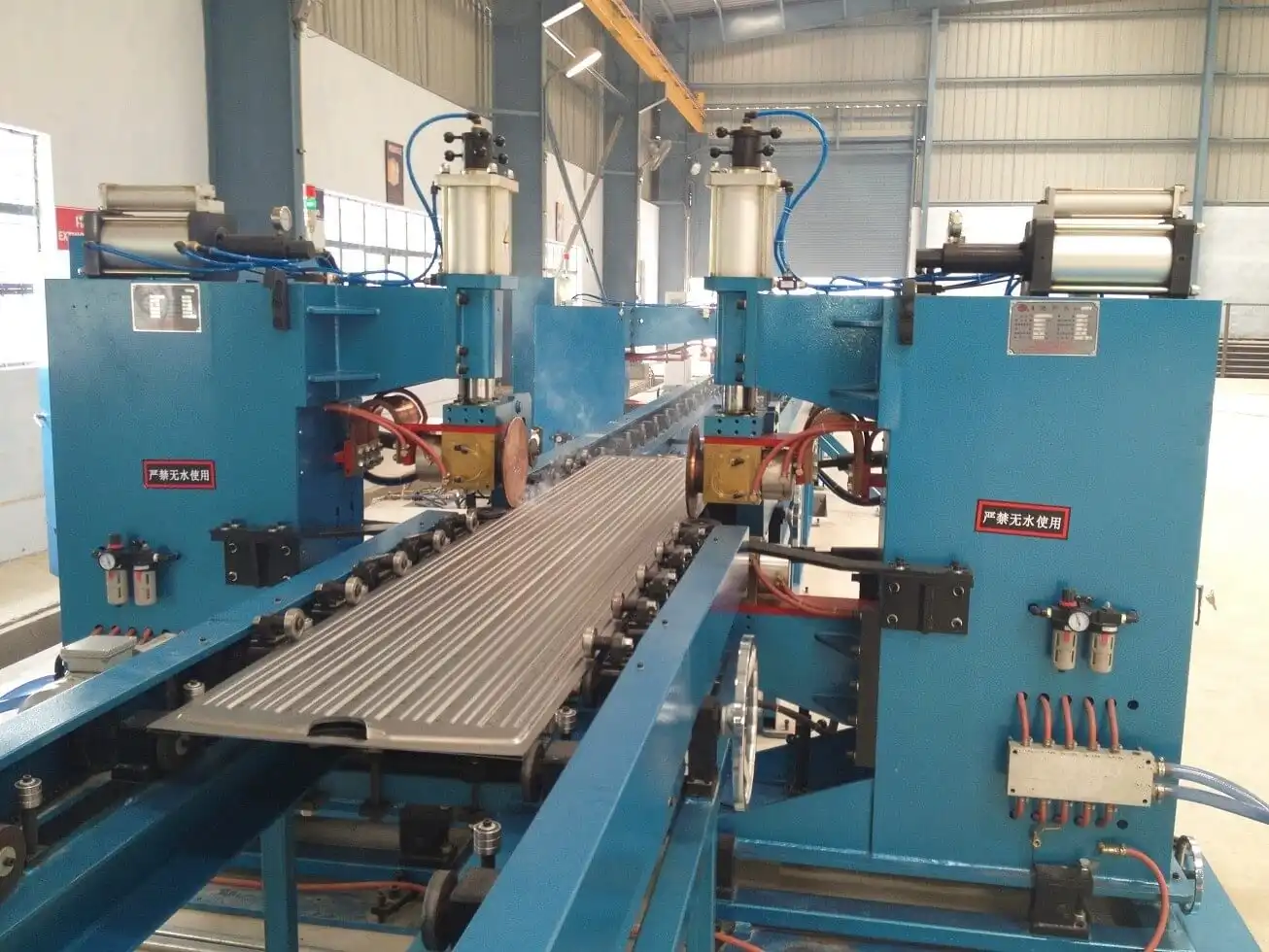
Double-sided seam welding station
2 sets of seam welding machines, symmetrically arranged
4 sets of seam welding pressure heads
2 sets of variable frequency welding power supplies
Power: 2 * 160 KVA
Max pressure: 12,000 N
Differential transmission mechanism
Seam welding speed: 0-2.8 m/min
Rolling shearing and leveling station
Composed of machine box, drive device, shearing device, edge crushing mechanism, leveling mechanism, electronic control system, pneumatic system, etc.
Rolling shear disc cuts both sides; cutter disc made of alloy tool steel (impact-resistant, wear-resistant, long service life)
Rolling shearing speed: 2-6 m/min
Driving power: 4 kW
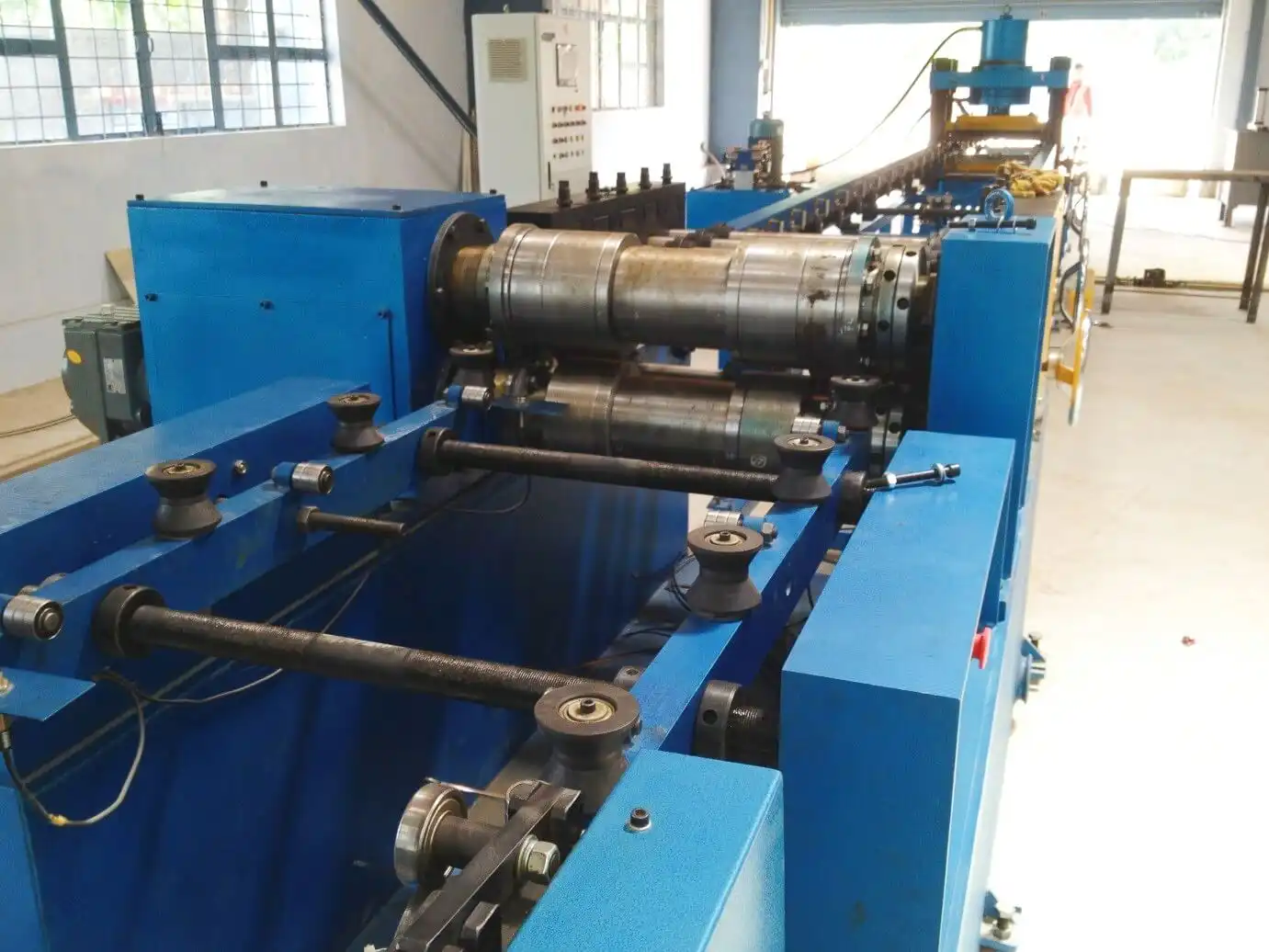
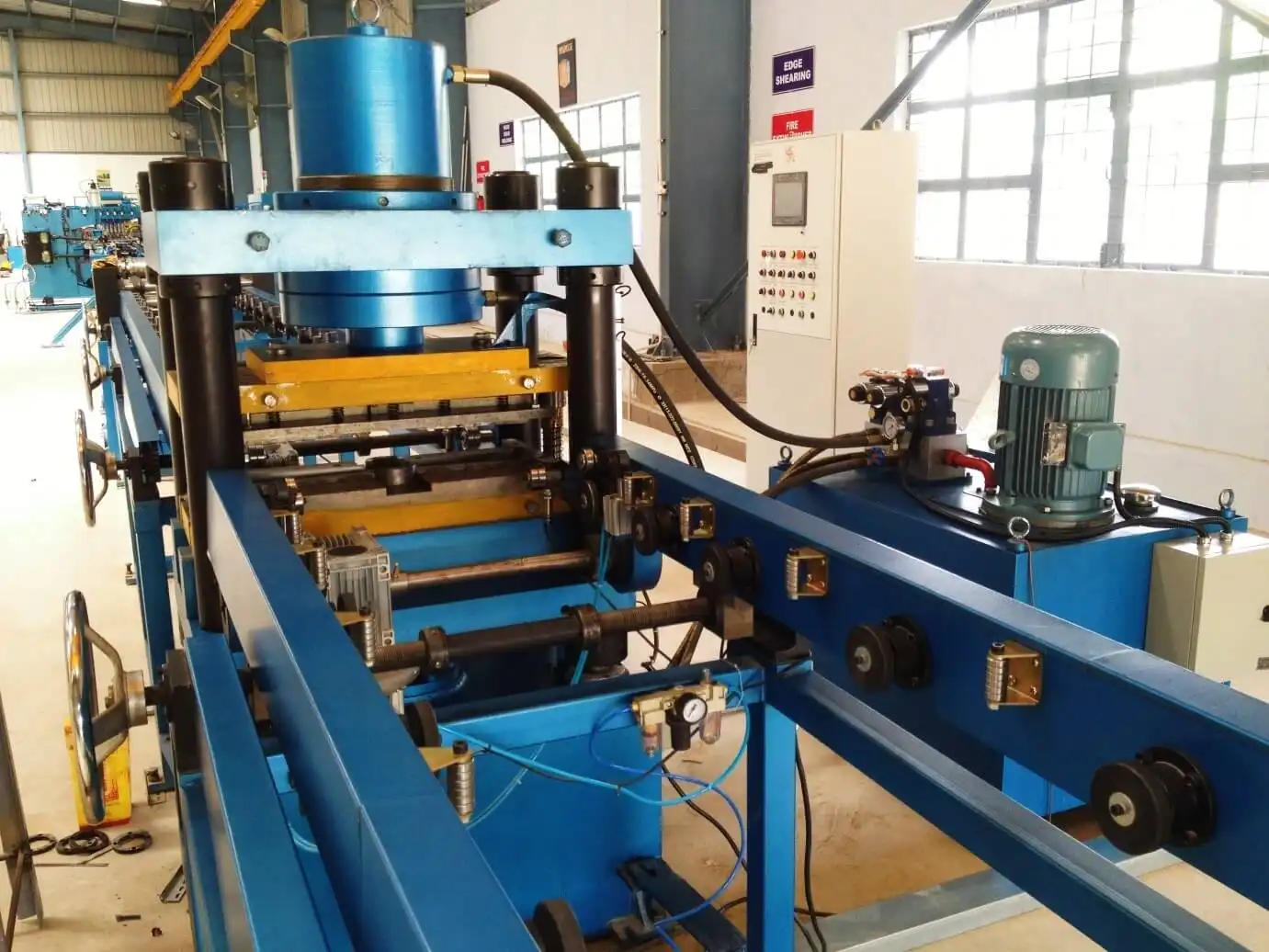
End punching station
Composed of base, lifting mechanism, punching frame, punching die, punching cylinder, lifting cylinder, and hydraulic station
Used for shearing loose ends to ensure edge alignment and consistency
Punching die with beveled edge to reduce punching force
Punching machine pressure: 160 T
End argon arc welding station
2 sets of equipment, arranged symmetrically
1 set for welding front end, 1 set for welding rear end of workpiece
4 sets of Panasonic argon arc welding power supplies
Current range: 5-315 A
Welding speed: 300-600 mm/min
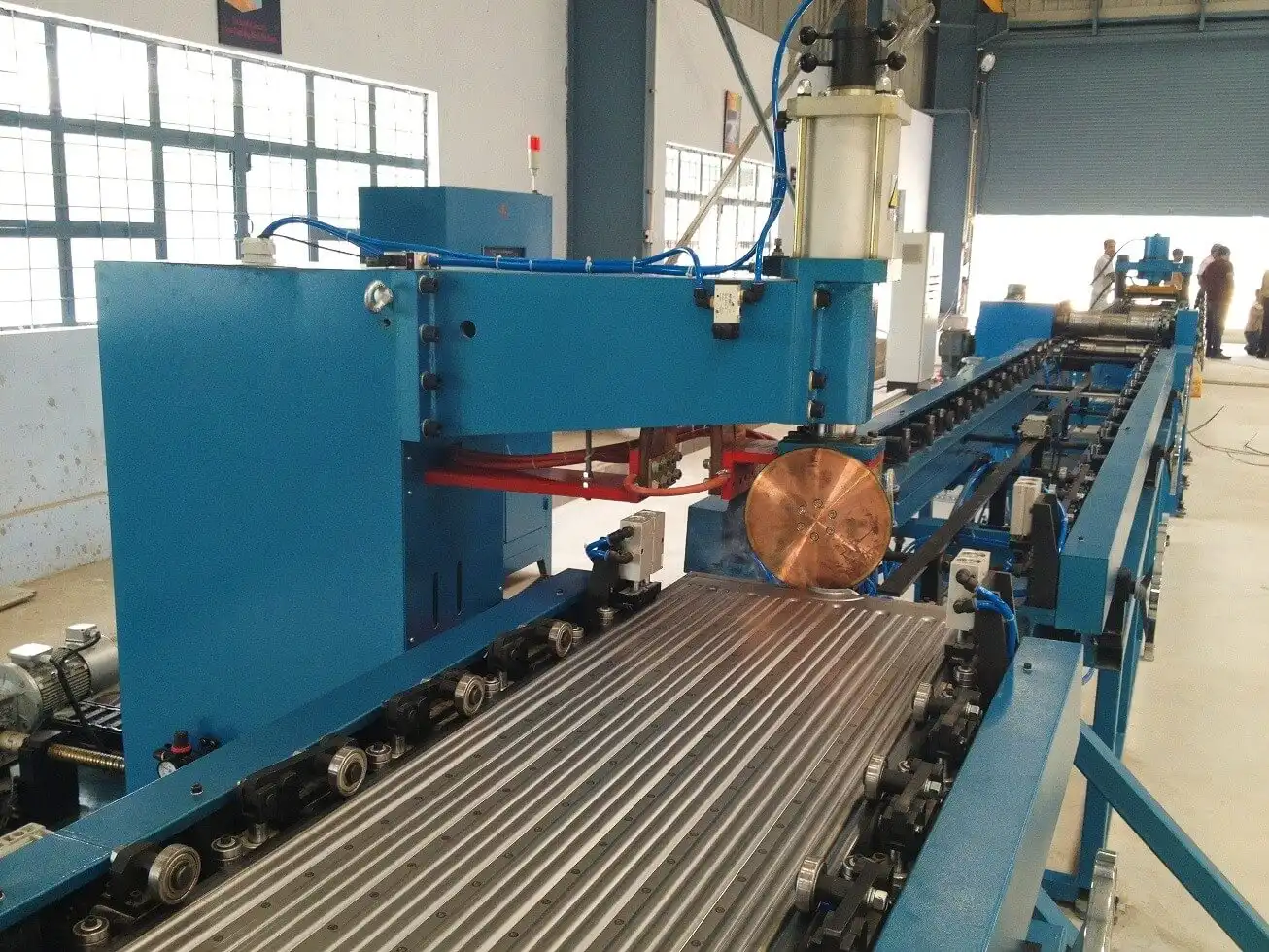
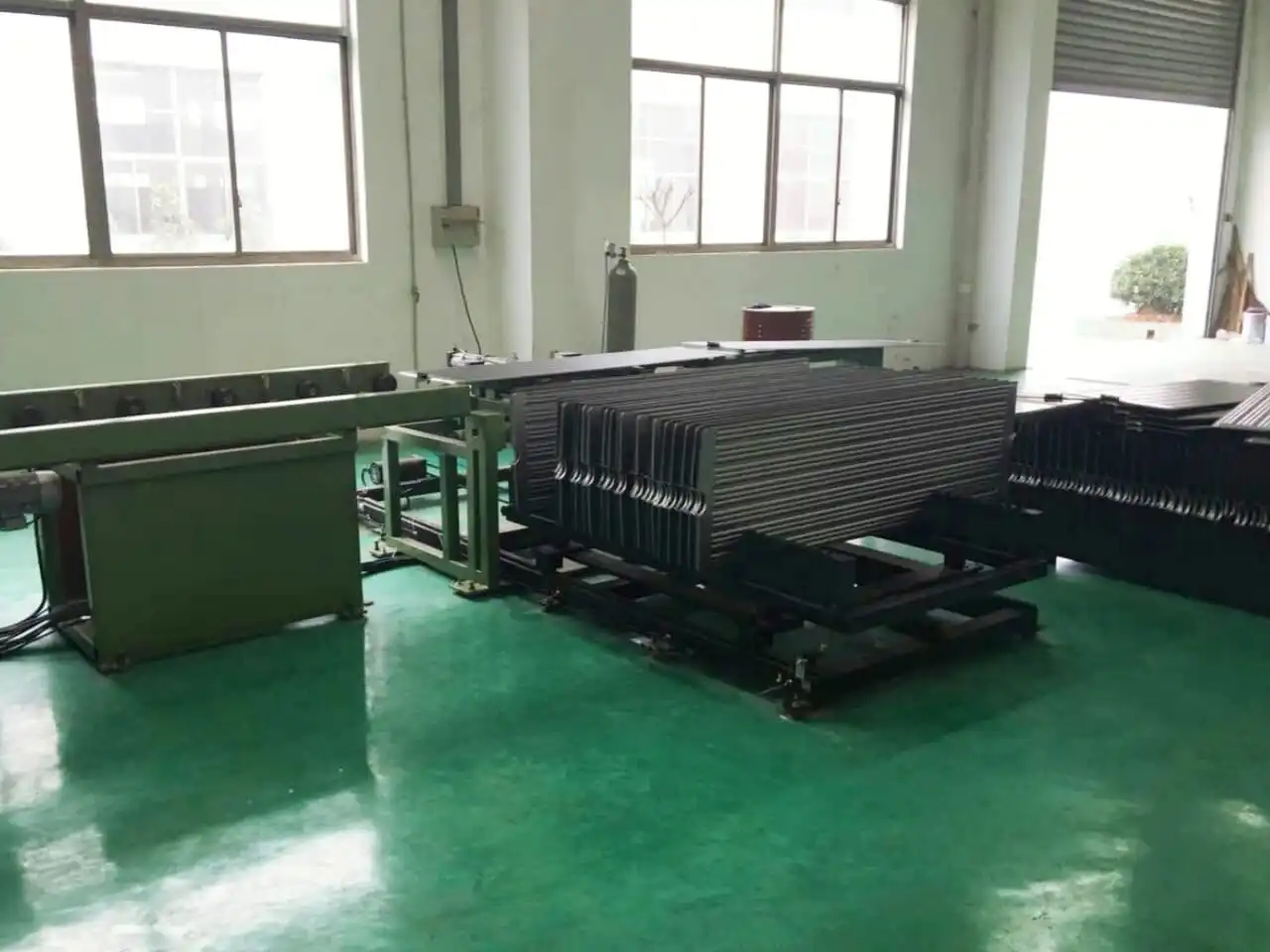
Palletizing station
Storage qty per palletizing rack: 40 pcs
Pallet spacing: 45 mm
Grabbing method: Cylinder clamps material, gripper turns 90° to place on rack
Material cart working method: Servo stepping movement, moves to next position after placing 1 piece, manual cart replacement when rack is full
Optional accessory machines
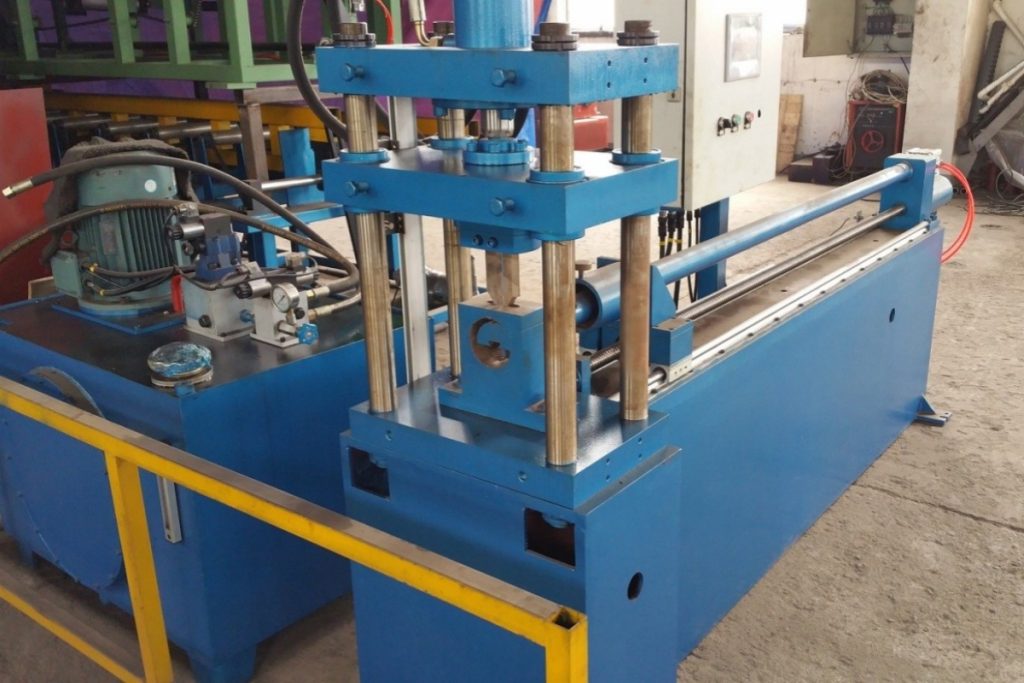
Header pipe punching machine
The Header Punch Machine automatically indexes to create up to 40 slot pairs on a pipe (max 40 panels). The pipe is cut with 2 specially shaped rectangular slots per panel. Internal support prevents deformation during punching. Cycle time per punch: ~6 seconds.
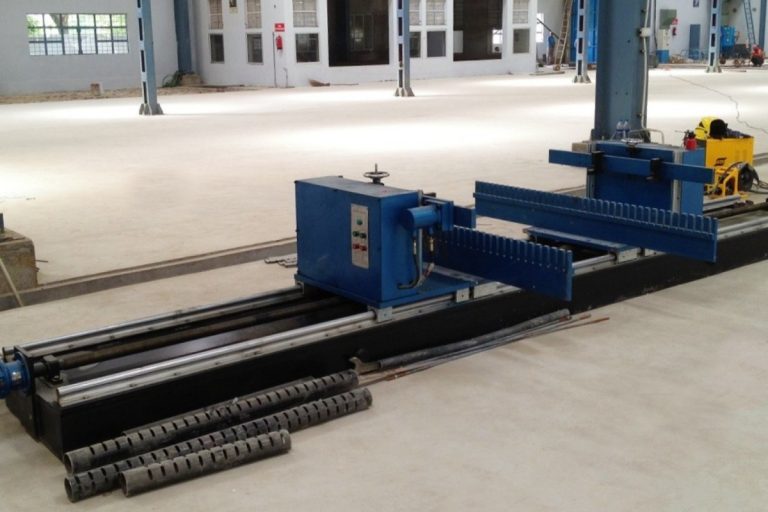
Assembly Fixture
The Horizontal Assembly Fixture aids in assembling radiator panels to header pipes. Panels are placed in a rack fixture at the Automated Stacking Machine and then into the fixture. One end is manually adjusted for length, while the other end uses a hydraulic press to hold and position for tack welding.
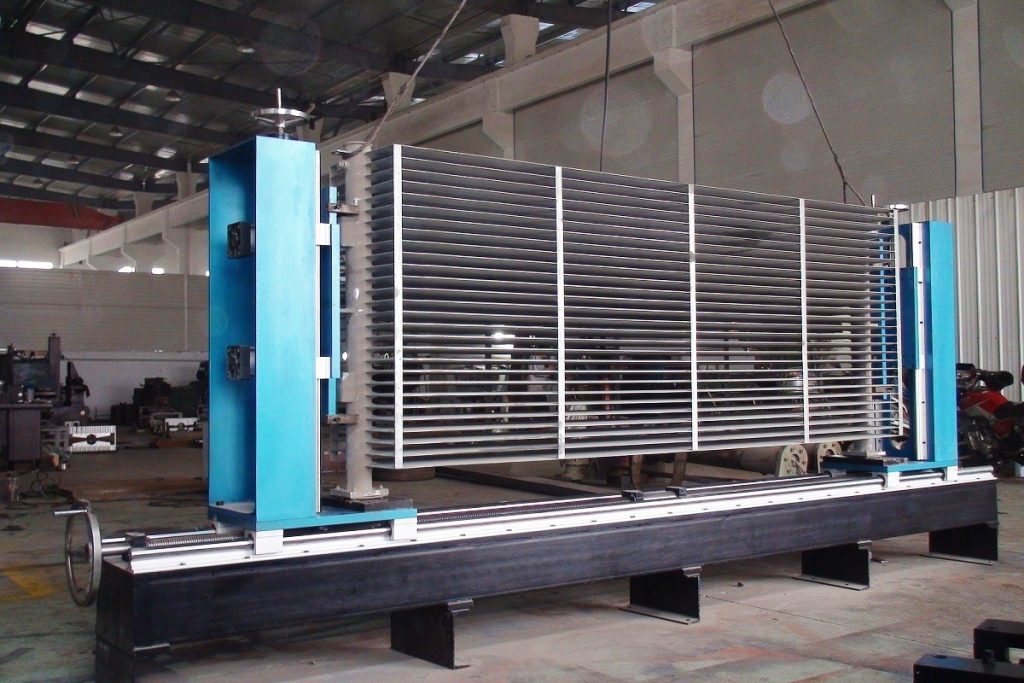
Flange welding table
The powered flange-mount fixture is designed to accurately align mounting flanges on the radiator centerline. With powered adjustments for panel length and assembly depth, it allows quick reconfiguration for production changes. Servo motor positioning ensures precise assemblies.
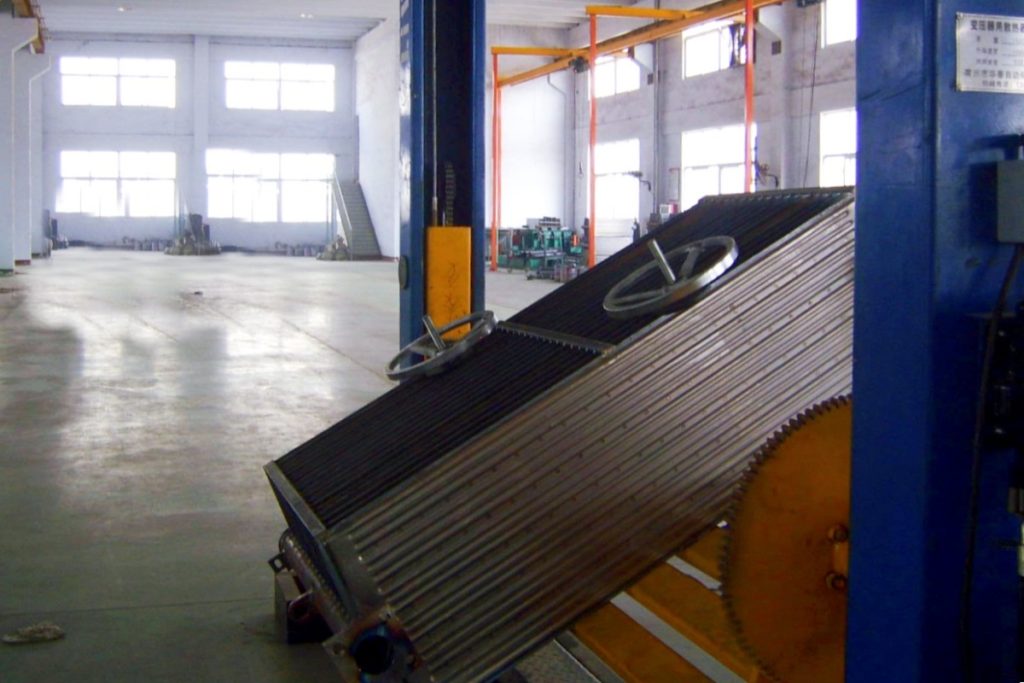
Turn over table for assembling welding
The powered turnover fixture is designed to turnover the radiator elements for the radiator assembly, after welding the header pipe from one side, then turnover the radiator to weld another side.
Other informations
Product Details
Trintfar Horse Transformer Radiator Fin Production Line meets international standards and offers a more economical and competitive price.
Fully Automatic Transformer Radiator Fin Production LineLayout Diagram
Production Results
Equipment Configuration List
No | Name | Model | Qty | Unit |
1 | Automatic unwinding machine | FJJ-0-0 | 1 | Set |
2 | Rolling forming shearing machine | CXJ-0-0 | 1 | Set |
3 | Turning and assembling machine | FZJ-0-0 | 1 | Set |
4 | Double-head pre-spot welding machine | DN60-2C | 1 | Unit |
5 | Gantry 12-head spot welding machine | LM-12C | 1 | Unit |
6 | Double-side seam welding machine | 2*FVM160-2C | 1 | Unit |
7 | Rolling and leveling machine | JPJ-0-0 | 1 | Unit |
8 | End punching machine | CQJ-0-0 | 1 | Unit |
9 | End argon arc welding machine | YHH-4C | 2 | Unit |
10 | Finished product stacking machine | MDJ-0-0 | 1 | Unit |
11 | Conveyor rack | SSJ-0-0 | 10 | Unit |
Control system List
Pneumatics | Airtac |
Control | Mitsubishi or Siemens |
Servo Systems | Yaskawa |
Linear Bearings & Actuators | THK |
Hydraulic | Yuci |
Electrical | Schneider, Siemens |
Technical Services
Adhere to customer-centricity and provide your company with comprehensive pre- sales and after-sales services such as installation, commissioning, training, and maintenance.
Pre-sales service: Before signing the contract, the company provides customers with various production process solutions and technical consulting services for equipment.
Installation and commissioning: According to the contract, our company will safely transport the equipment to the installation site designated by the user within the specified time, and send technical service engineers to install it on site. When the user has the basic installation and commissioning spare parts, the technical service engineer will install and debug the machine for the user to use, ensuring that the installation and commissioning site environment is neat, clean and orderly.
After-sales Training: The company offers free technical training (min. 5 days) at the buyer’s site or the seller’s training center. Key topics include:
- -Control software usage
- -Power on/off procedures
- -Panel and software parameter settings
- -Basic machine cleaning and maintenance
- -Handling common hardware failures
- -Operational precautions
Equipment maintenance
- -One-year warranty after final acceptance;
- -Customer service response time is within 24 hours;
- -Paid repairs are provided after the warranty period.