Oven Production Line
The Oven Production Line is designed for high-efficiency steel panel radiator production, featuring advanced technology for superior welding, reliability, and ease of use.
The steam oven liner welding line is customized to meet production needs, offering fast welding, and continuous 24-hour operation.
- Machinery Capacity: 25s-40s/Pcs
- Precision Welding: Double welding heads for consistent results
- Robust Build: Durable, handles heavy production demands
- Advanced Automation: Fully automatic, reducing labor and time
- Versatile Compatibility: Works with metal cutting, engraving, forging, and polishing machines.
Product Descriptions
Workflow
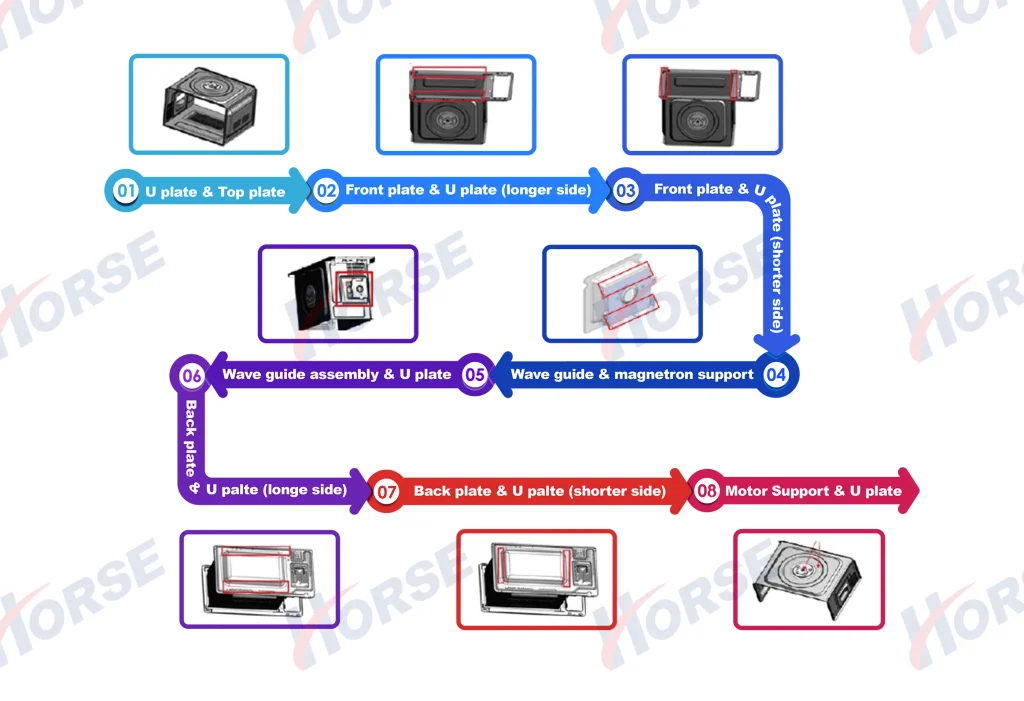
Work flow:U plate & Top plate → Front plate & U plate (longer side) → Front plate & U plate (shorter side) → Wave guide & magnetron support → Wave guide assembly & U plate → Back plate & U palte (longe side) → Back plate & U palte (shorter side) → Motor Support & U plate
Main equipments
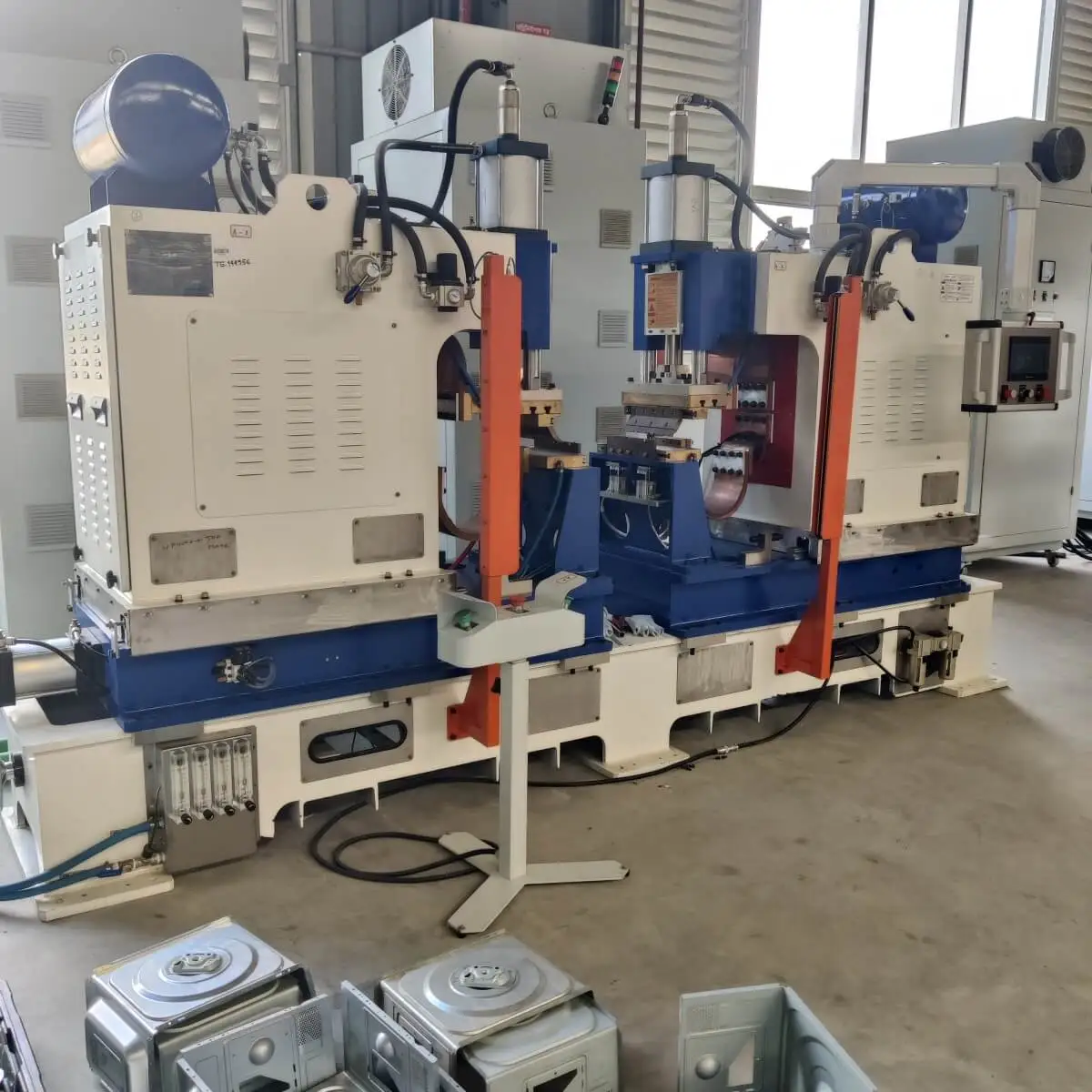
U plate and top plate welding
Equipment model: 2xDR-20000J-2C
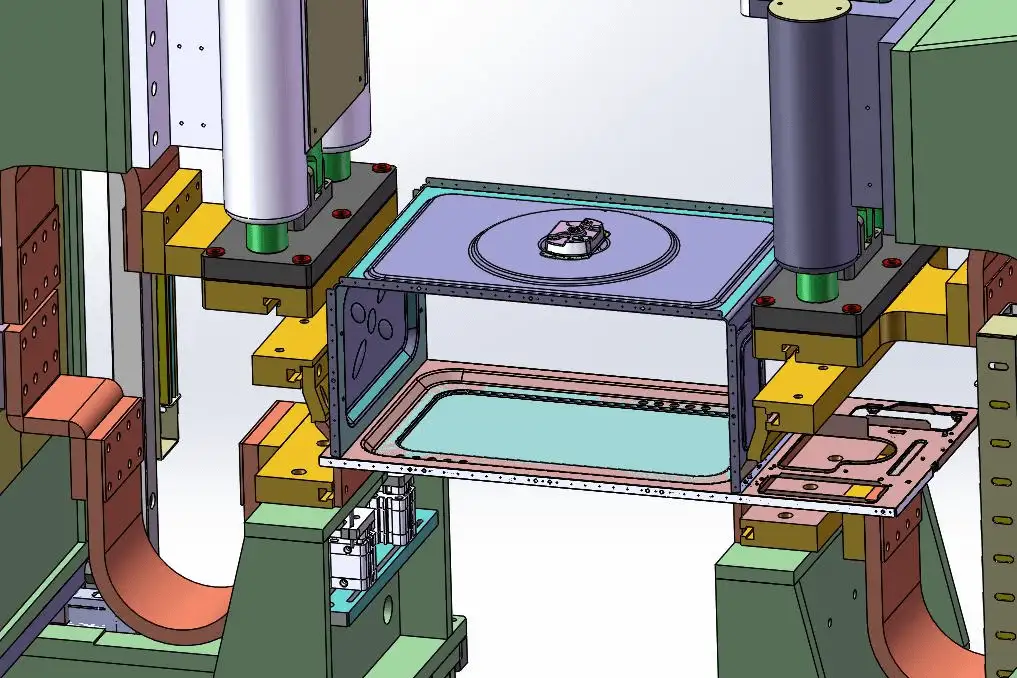
U board and front board short side welding
Equipment model:2xDR-13000J-2C
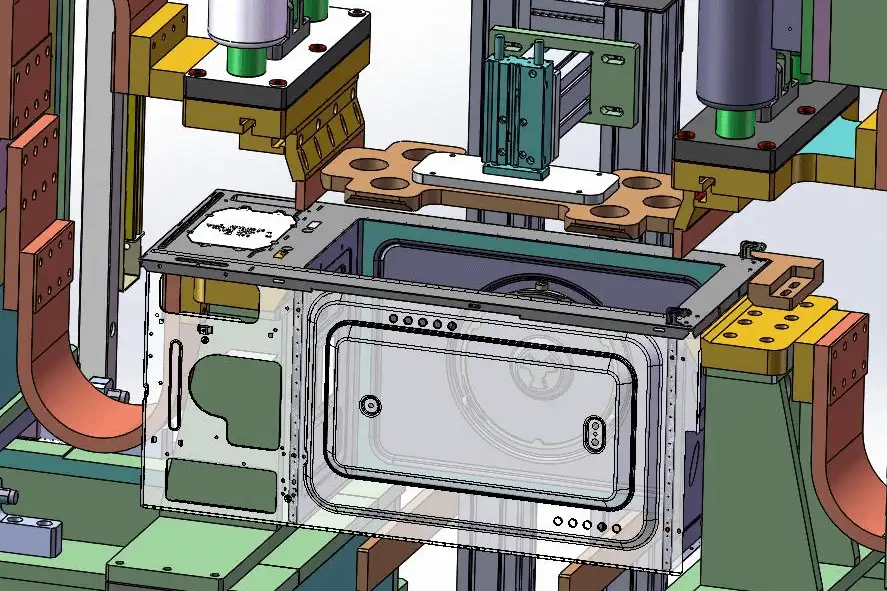
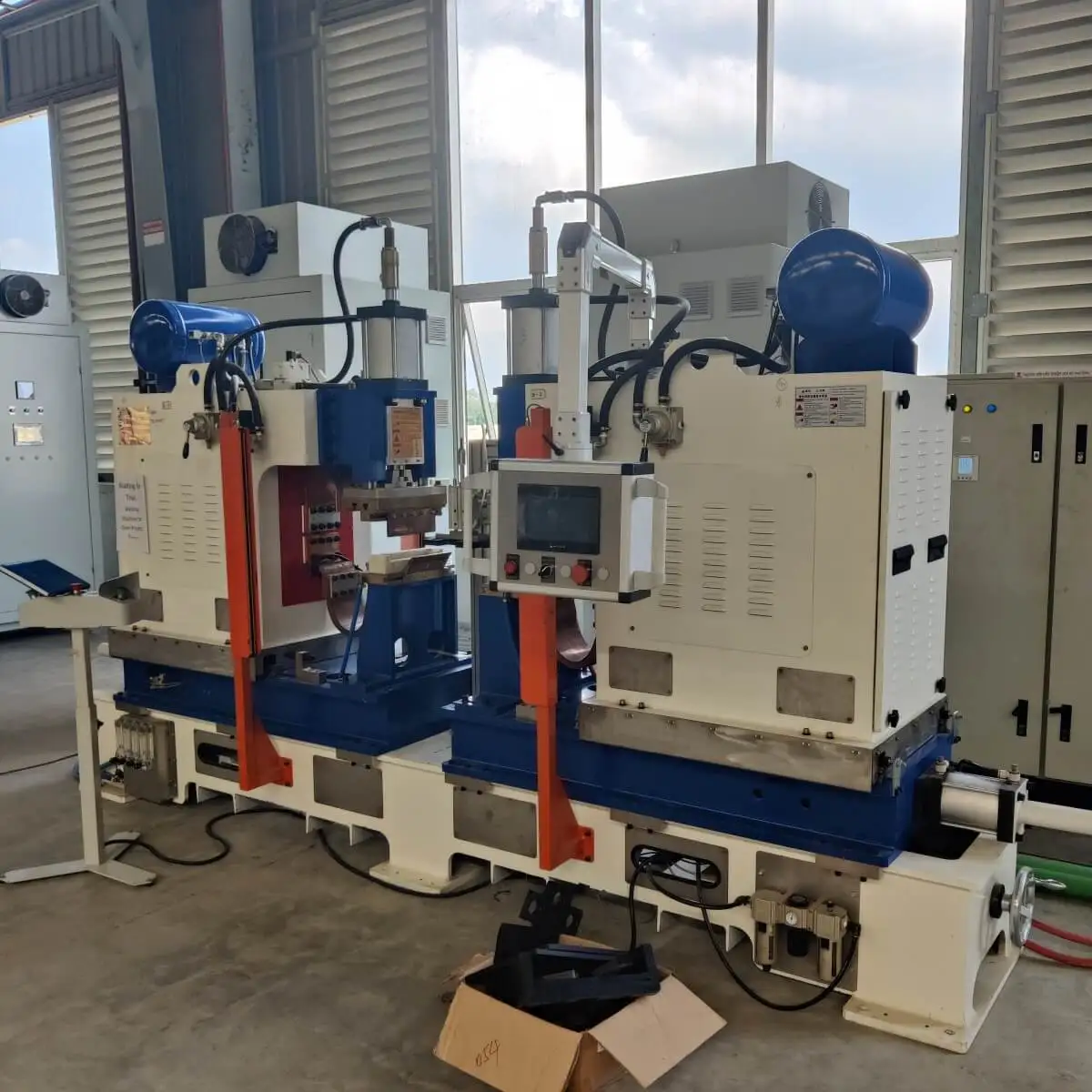
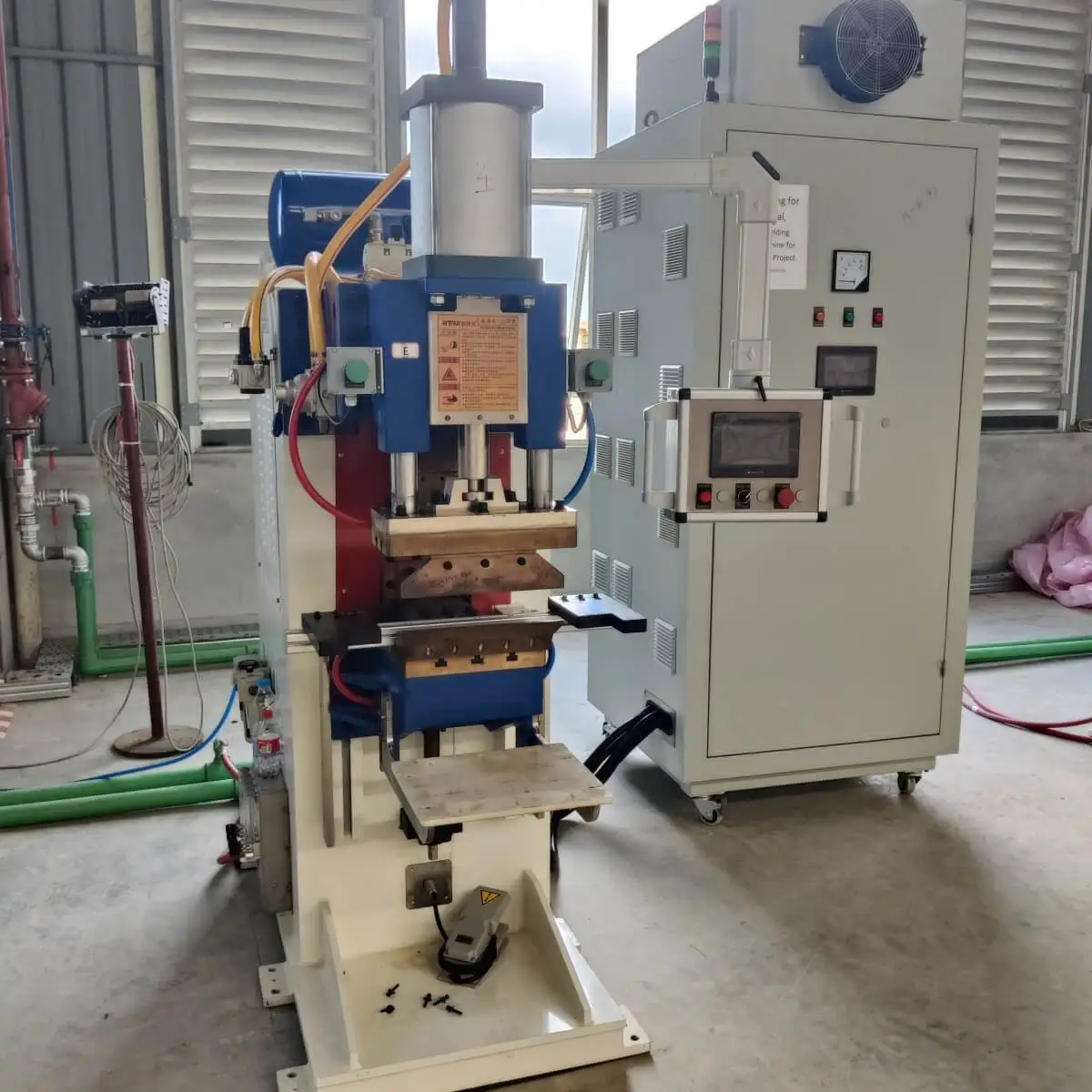
U board and front board long side welding
Equipment model:DR-20000J-1C
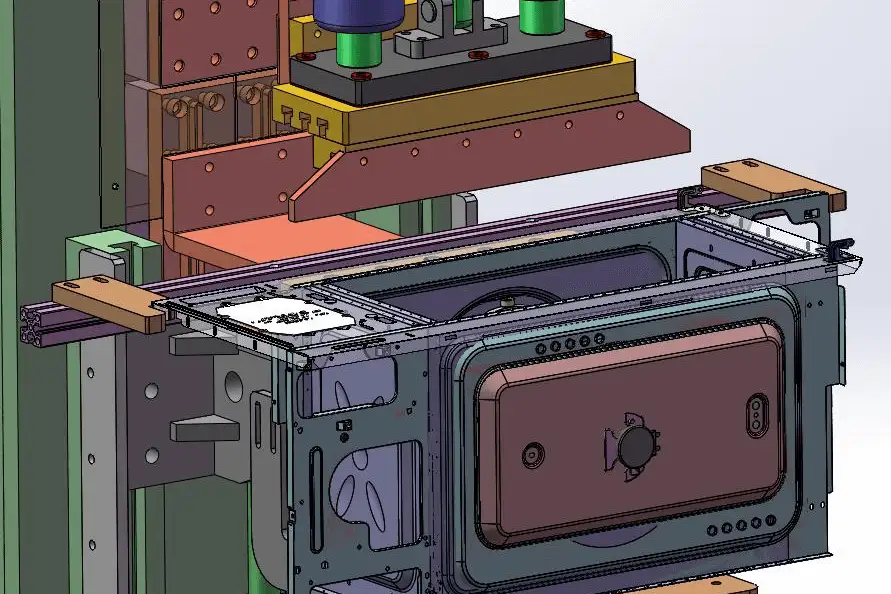
Waveguide Box and Magnetron Welding
Equipment model:DR-30000J-1C
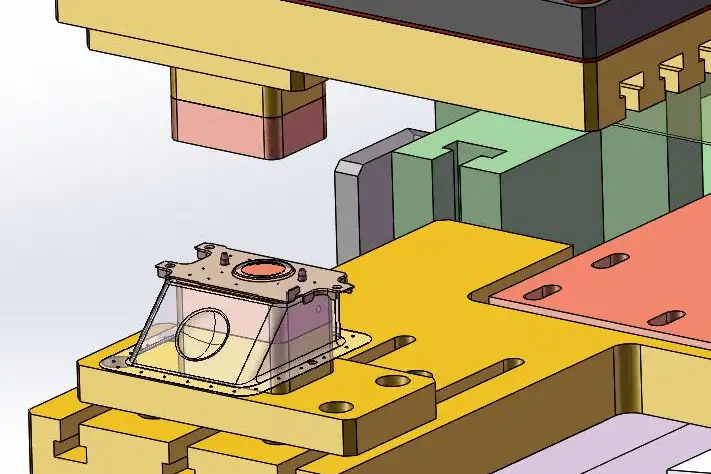
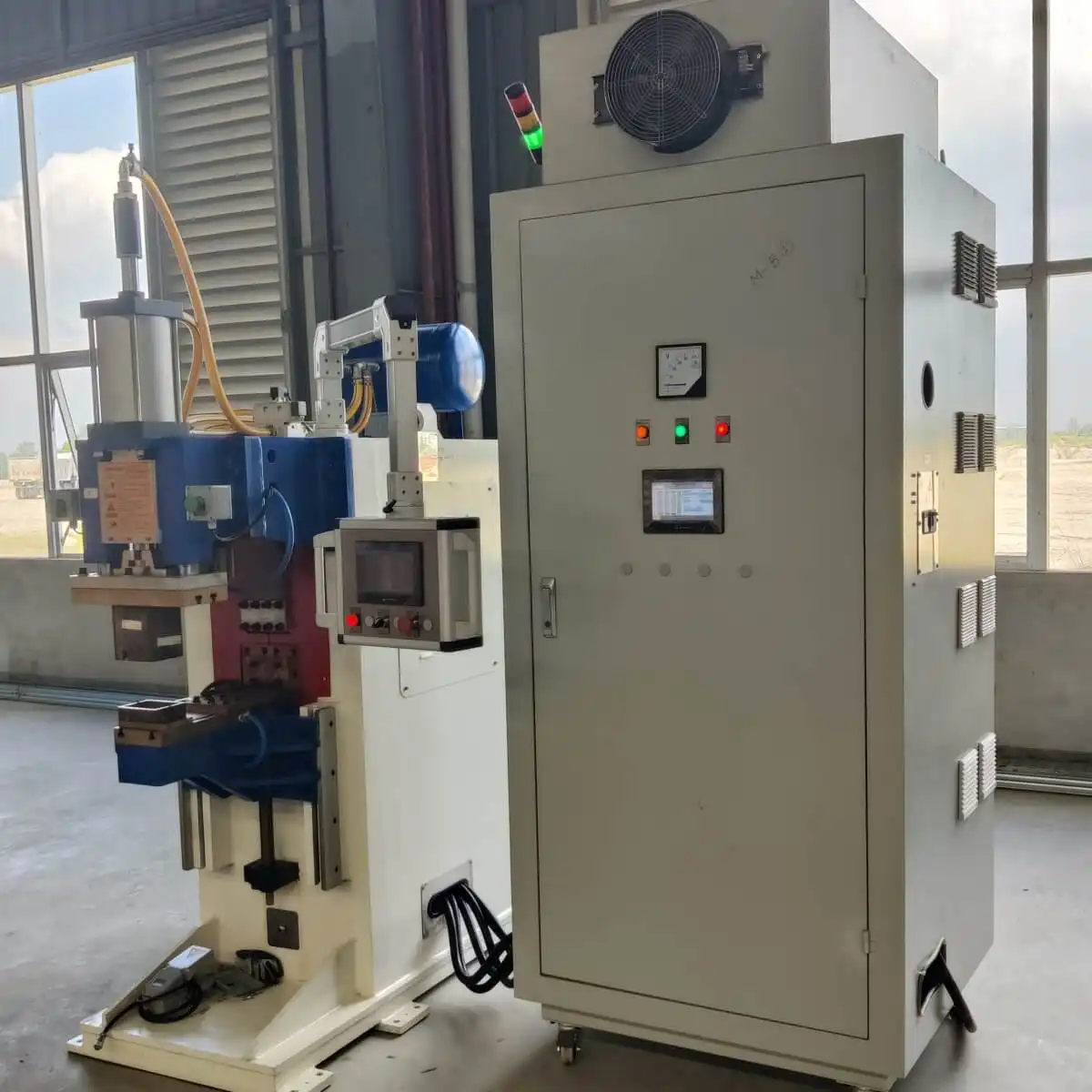
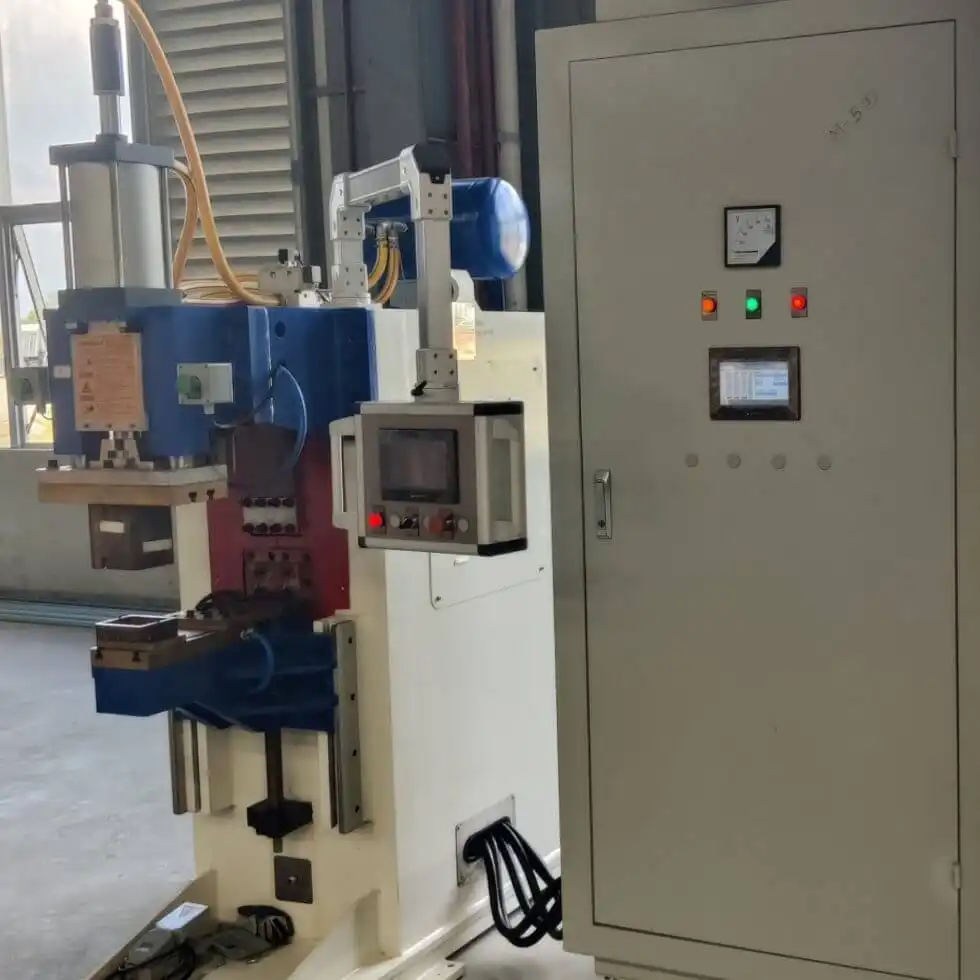
Waveguide Assembly and U Plate Welding
Equipment model:DR-30000J-1C
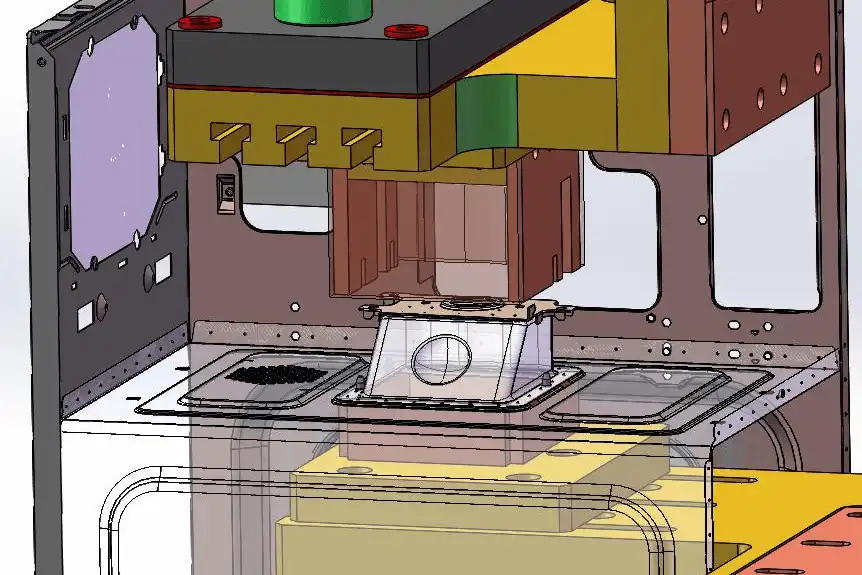
welding the long side of the back plate with the U plate
Equipment model:DR-20000J-1C
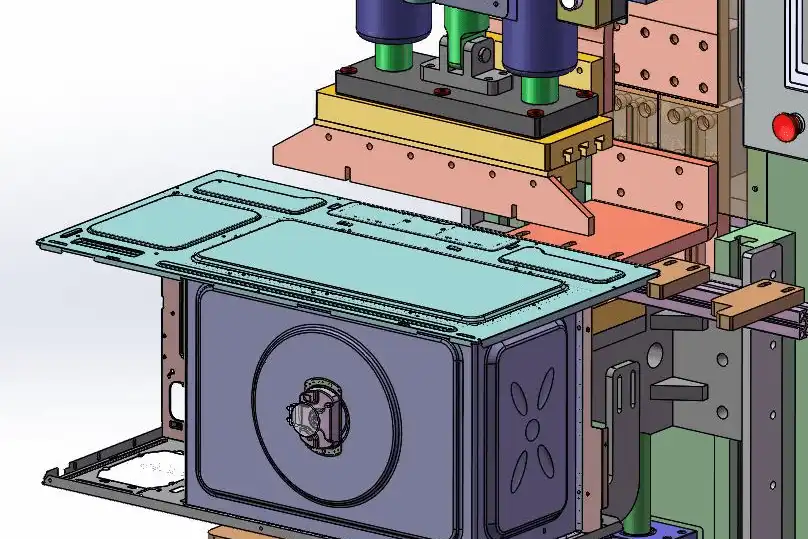
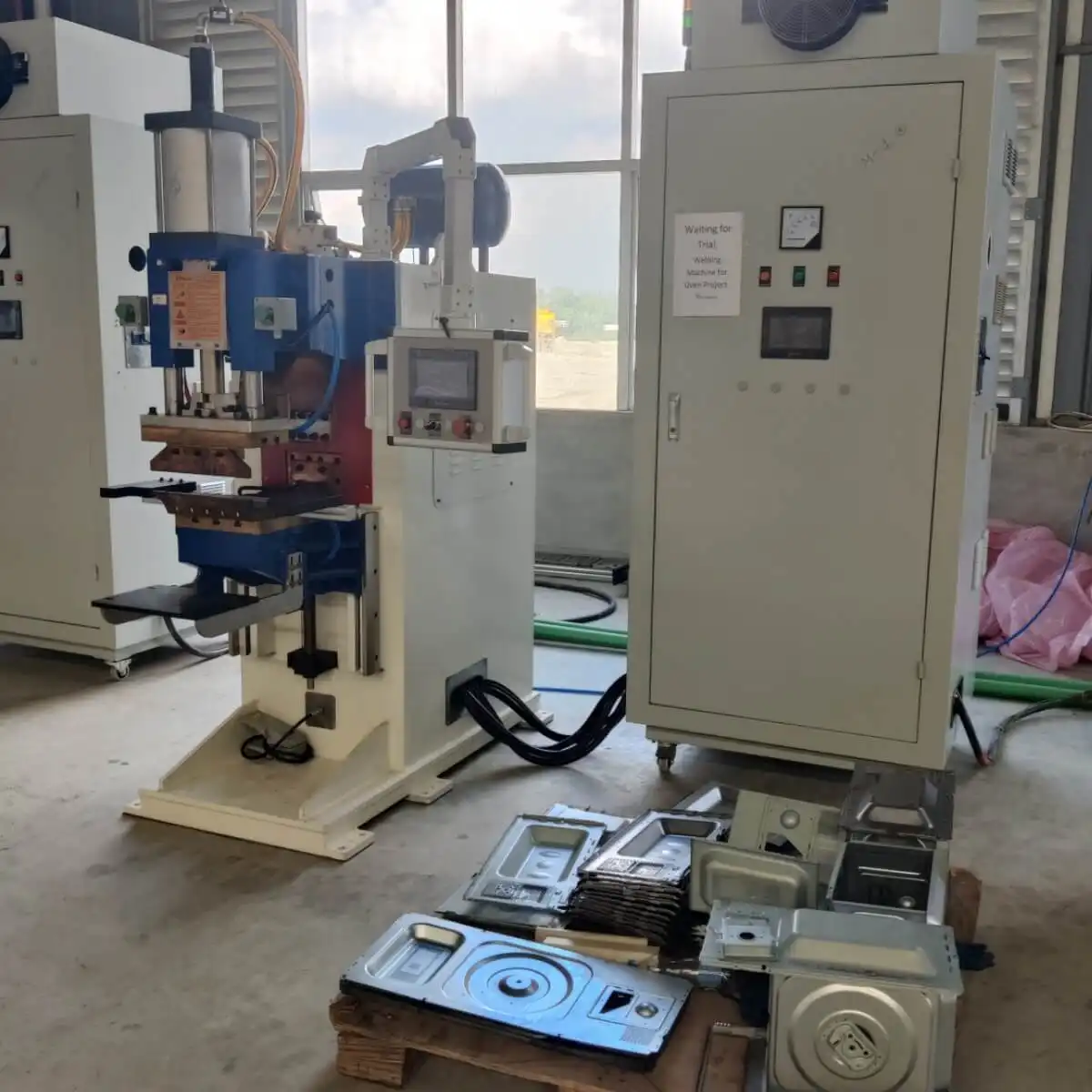
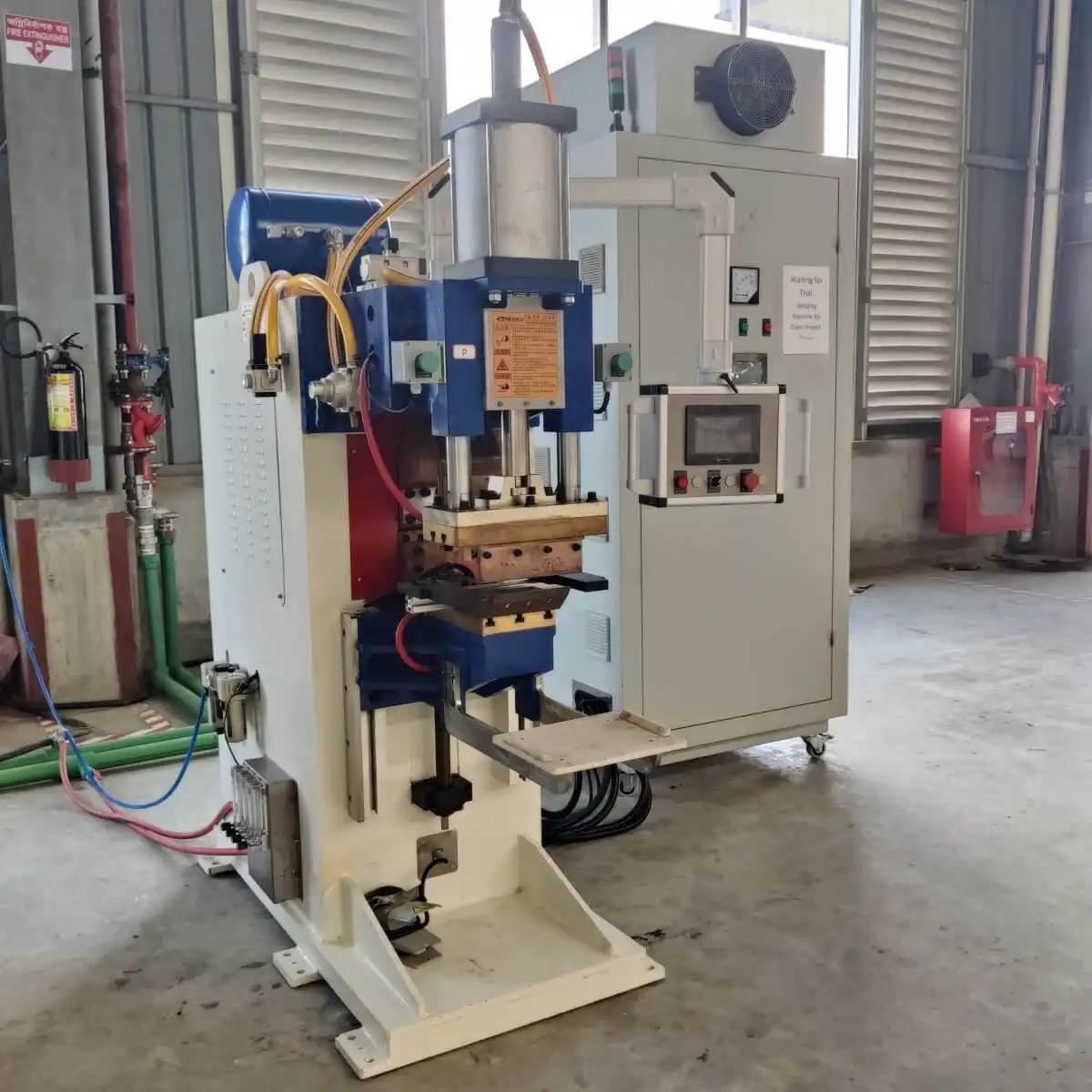
short side of the back plate and U plate welding
Equipment model:DR-13000J-1C
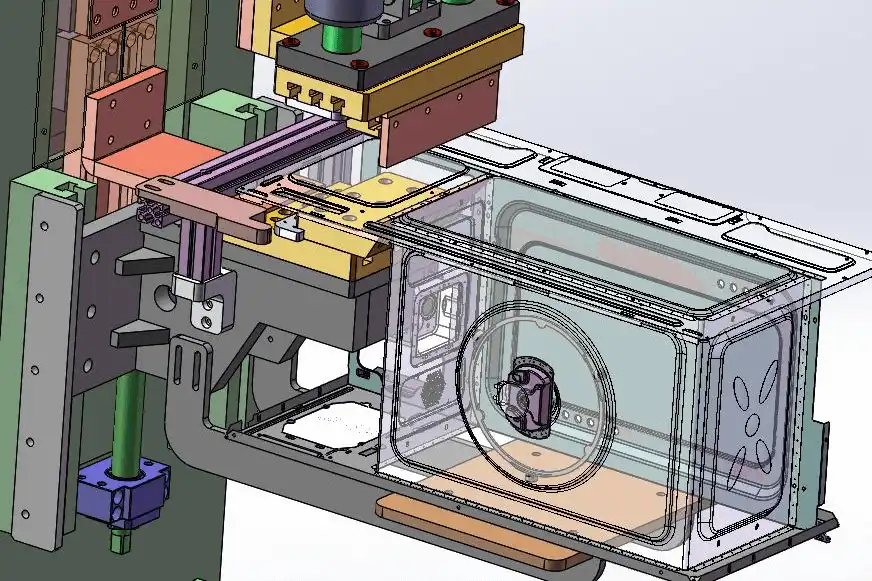
motor support welding
Equipment model: DR-13000J-1C
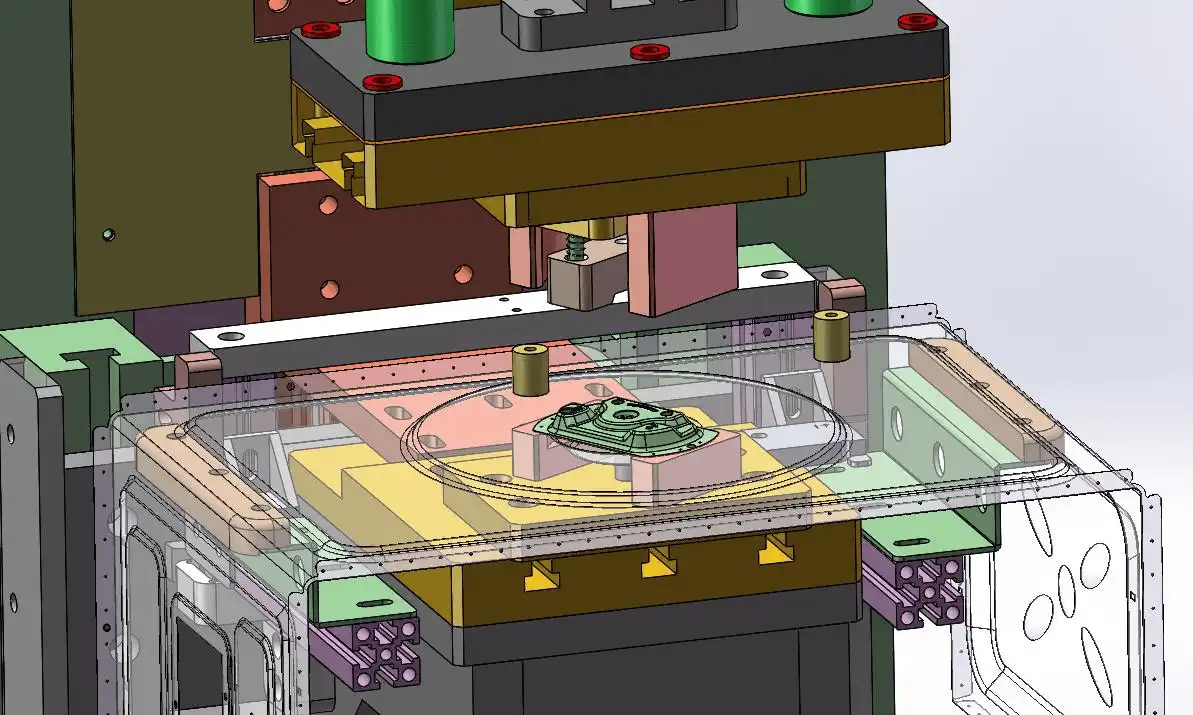
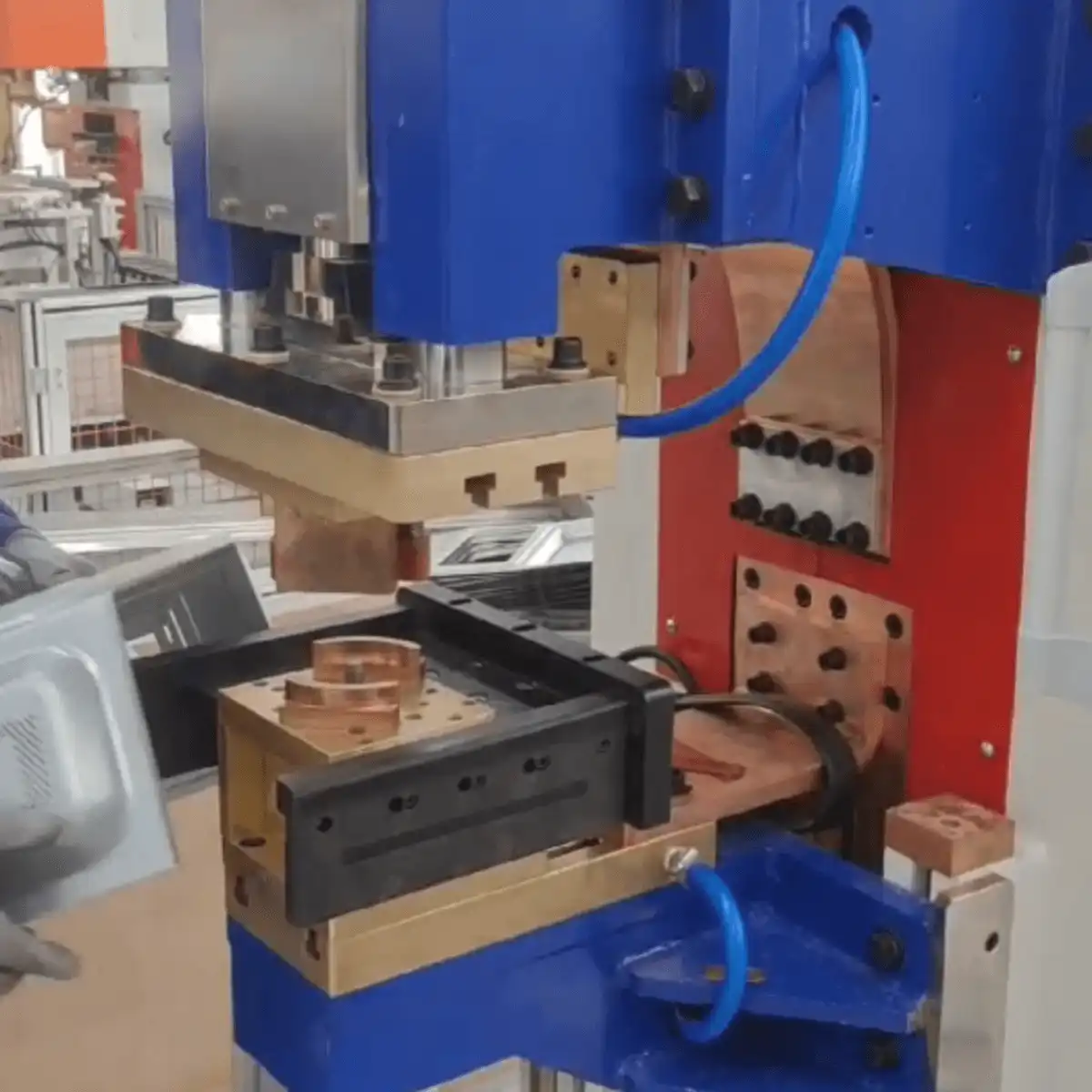
Other informations
Product Details
Oven Production Line Layout Diagram
Production Results
Basic Structure of DR-20000J Capacitor Energy Storage Spot Welding Machine
Components:
Frame, Pressurizing Mechanism, Water Cooling System, Welding Circuit, Capacitor Power Supply, Control System, Body, Welding Cylinder, Electrodes, Cooling Circuit, Monitoring Device, and Safety Mechanism.
- Frame:
- C-frame structure, high-quality steel, and section steel.
- Precision machining and heat treatment for rigidity and accuracy.
- Pressurizing Mechanism:
- Vertical pressure type with self-lubricating bearings for better performance.
- Minimizes electrode impact, preventing damage and wear.
- Pneumatic System:
- Includes Japanese “SMC” solenoid valves, Taiwanese air processors, and oil-free cylinders.
- Gas storage tank stabilizes pressure.
- Discharge Transformer & Welding Circuit:
- Uses Wugang silicon steel sheets, and precision copper casting.
- Soft copper tape and electrodes in series.
- Main Control System:
- Mitsubishi PLC and HMI.
- Manual, automatic, and charging modes.
- Adjustable parameters via touch screen (voltage, pressure time).
- Welding Controller:
- Fast charging/discharging via microprocessor.
- Compatible with old and new capacitors, it extends capacitor life.
- Protection modes for fault prevention.
- Automatic adjustment for capacitor voltage and leakage current.
- Fault detection for overcharge, discharge, and capacitor errors.
- Stores up to 5 welding specs, count 9999 welds, real-time voltage detection (error ≤ 1%).
Equipment Configuration List
No | Station Name | Model | Quantity | Unit |
1 | Motor bracket welding | DR-13000J-1C | 1 | Set |
2 | U board and top board welding | 2xDR-20000J-2C | 1 | Set |
3 | U board and front board short-side welding | 2xDR-13000J-2C | 1 | Set |
4 | U board and the long side of the front board are welded | DR-20000J-1C | 1 | Set |
5 | Waveguide box and magnetron welding | DR-30000J-1C | 1 | Set |
6 | Waveguide assembly and U-board welding | DR-30000J-1C | 1 | Set |
7 | The long side of the back plate is welded to the U plate | DR-20000J-1C | 1 | Set |
8 | The short side of the back plate is welded to the U plate | DR-13000J-1C | 1 | Set |
Technical Services
Adhere to customer-centricity and provide your company with comprehensive pre- sales and after-sales services such as installation, commissioning, training, and maintenance.
Pre-sales service: Before signing the contract, the company provides customers with various production process solutions and technical consulting services for equipment.
Installation and commissioning: According to the contract, our company will safely transport the equipment to the installation site designated by the user within the specified time, and send technical service engineers to install it on site. When the user has the basic installation and commissioning spare parts, the technical service engineer will install and debug the machine for the user to use, ensuring that the installation and commissioning site environment is neat, clean and orderly.
After-sales Training: The company offers free technical training (min. 5 days) at the buyer’s site or the seller’s training center. Key topics include:
- -Control software usage
- -Power on/off procedures
- -Panel and software parameter settings
- -Basic machine cleaning and maintenance
- -Handling common hardware failures
- -Operational precautions
Equipment maintenance
- -One-year warranty after final acceptance;
- -Customer service response time is within 24 hours;
- -Paid repairs are provided after the warranty period.