Steel Drum Production Line
The steel drum production line is a fully automated system covering drum making, bottom and lid formation, spray painting, testing, and more. The high-speed seam welding machine uses a three-part power source: phase secondary rectifier, three-phase medium frequency inverter DC, and three-phase variable frequency AC, ensuring compatibility with various material specifications. Hard specifications in welding ensure stable and durable equipment.
Technical Solution
Complex pressing technology in Front Equipment saves 3-4% steel per 55-gallon drum.
7-layer circle rolling technology (core tech) used in Middle Equipment.
High-pressure airless painting and fuel heating in Post Production Equipment.
Drums meet UN Class 1 standard for Sea Transport of Dangerous Goods.
- Capacity config: 2-10 drums/min
- Operators: around 11 people
- Power Consumption:1 kWh/Drum
Product Descriptions
Workflow
-1024x516.webp)
Work flow:Rounding → Seam Welding → Bead/Flanging → Corugating/W Beading → Leakage Test (before seaming) → Seaming → Leakage Test (after seaming) → Clean Oil, Washing, Fe-Phosphorize, Washing → Washing Drying → Outside Painting → Drying After Outside Painting → Cooling → Warehousing (Offline)
Main equipments
Steel Drum Body Production Machines
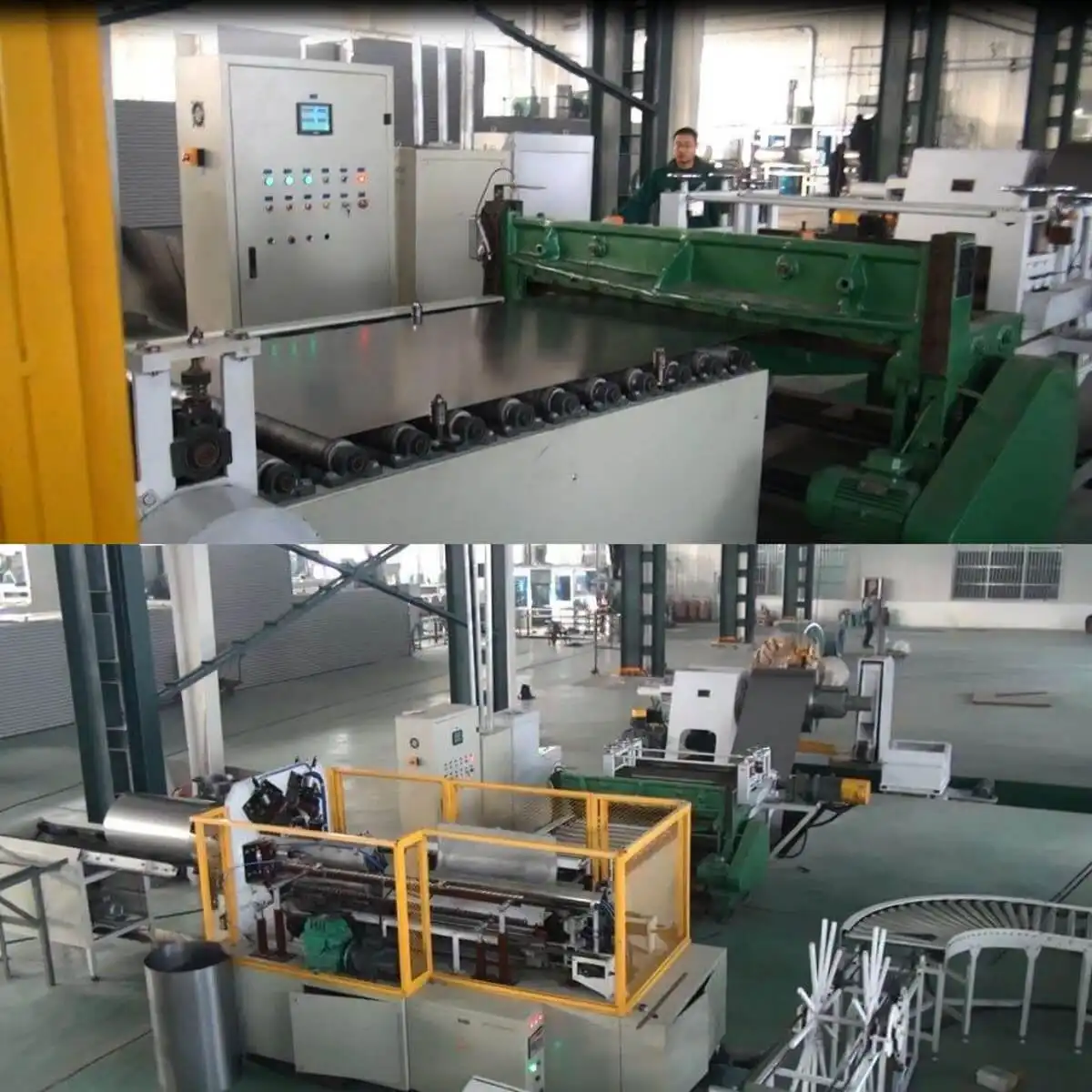
Drum Body Steel Sheet Production Machine
Coil Cart: 3-in-1 motor drive, hydraulic up/down
Uncoil Unit: Hydraulic drive, no power turning, coil diameter Ф508-Ф610mm, max load: 15 tons
7-Roller Leveler: 7 rollers, motor speed adjustable by frequency
Measurement Facility: Length precision via Japan-made A.C. service motor
Sheet Cutting Machine: 3*1500mm, PLC controlled
Transporter: Convey cutting sheets to auto welder
Drum Body Auto Welding Machine
Overlap Control: Guide bar positions drum; Z-bar ensures 2mm overlap with easy maintenance via detachable wear strips and a profiled nose for precise weld wheel contact.
Hour Glass Rolls: Mounted on “goal post” frame with sensors, ensuring gradual sizing, consistent overlap, and minimized surface marking; lower rolls pivot for maintenance, upper roll adjusts for size tolerance with pneumatic cylinders.
Weld Heads: SEW inverter-controlled AC motor with gearbox and pneumatic pressure for constant speed; weld wheels cross-indexed for even wear, auto-lubed, and can be manually or semi-automatically trimmed to reduce downtime.
Weld Head Cylinder Slide: Lower weld head mounted on light alloy ram with pneumatic cylinder and bellows spring to stabilize force and dampen reactions at weld start.
Welding Control: Energy-efficient three-phase AC, control with LCD display.
Transformer: SP 350KVA.
Planishing Rolls: Optional.
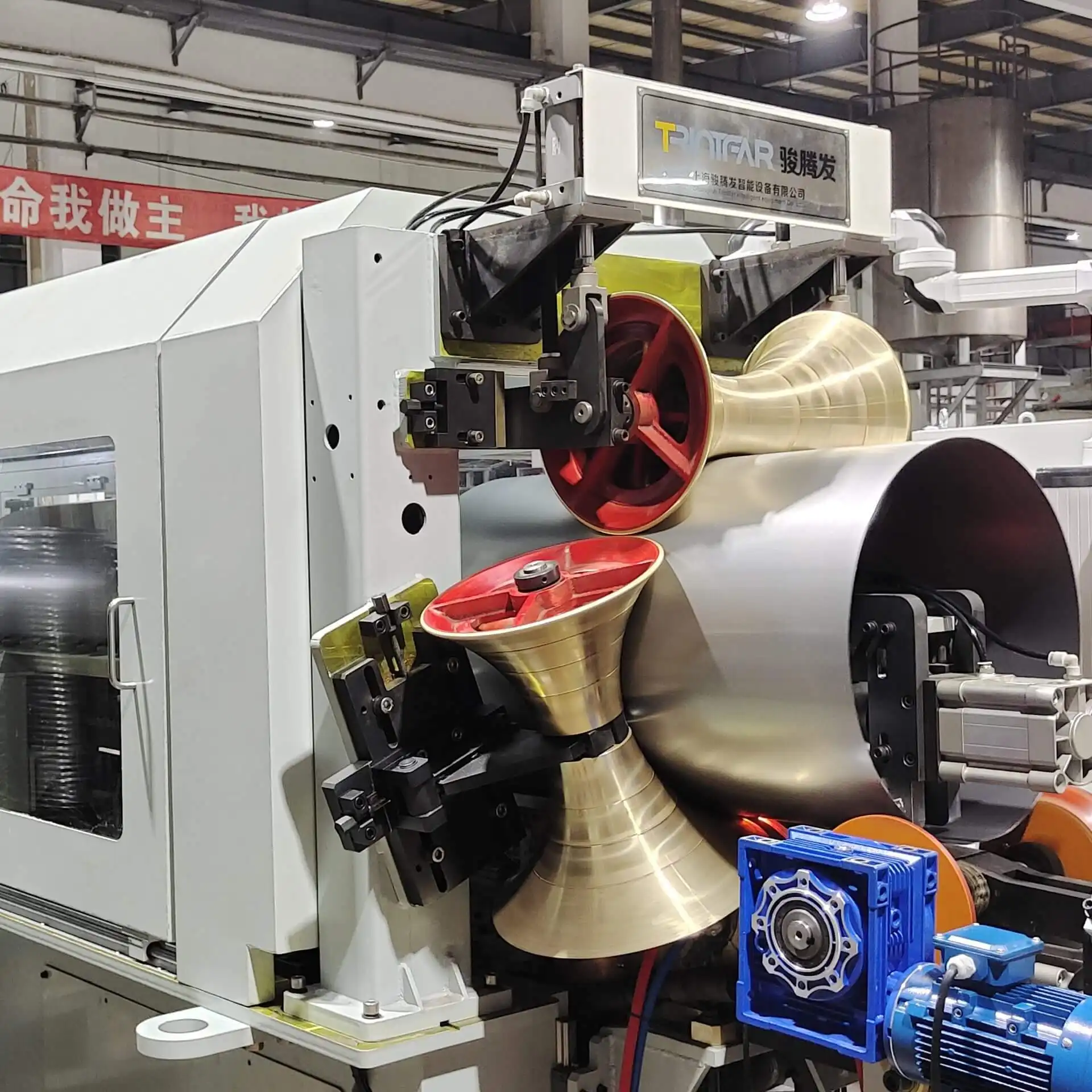
Flange Machine
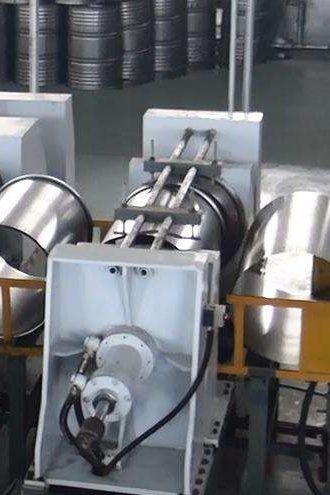
Higher efficiency flange formation. Suitable for cold-rolled steel, PLC controlled, hydraulic drive. Unit power: 22KW.
Beading Machine
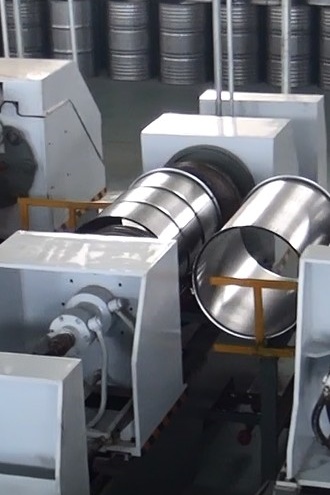
With 8 bevel molds moving outward to form 12mm adjustable beading. PLC controlled, hydraulic drive, unit power: 15KW.
Corrugating Machine
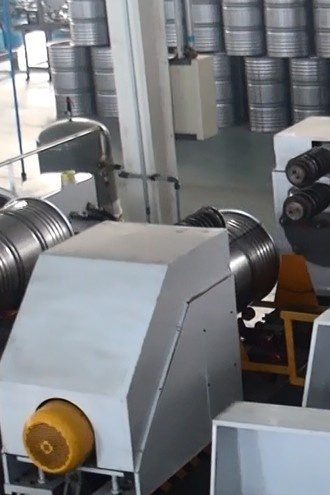
Higher efficiency flange formation. Suitable for cold-rolled steel, PLC controlled, hydraulic drive. Unit power: 22KW.
Seaming Machine
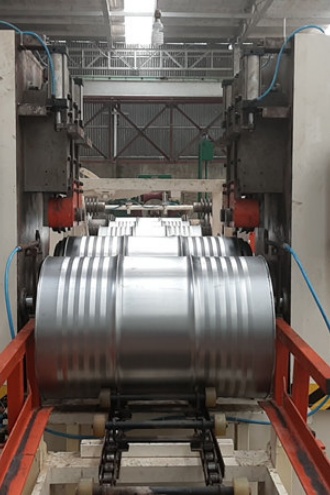
Auto load press and seam welding. Double motors and main shafts. Cam mechanism roll wheels , easy to adjust, PLC controlled. Unit power: 41KW.
Steel drum bottom & top cover production Machines
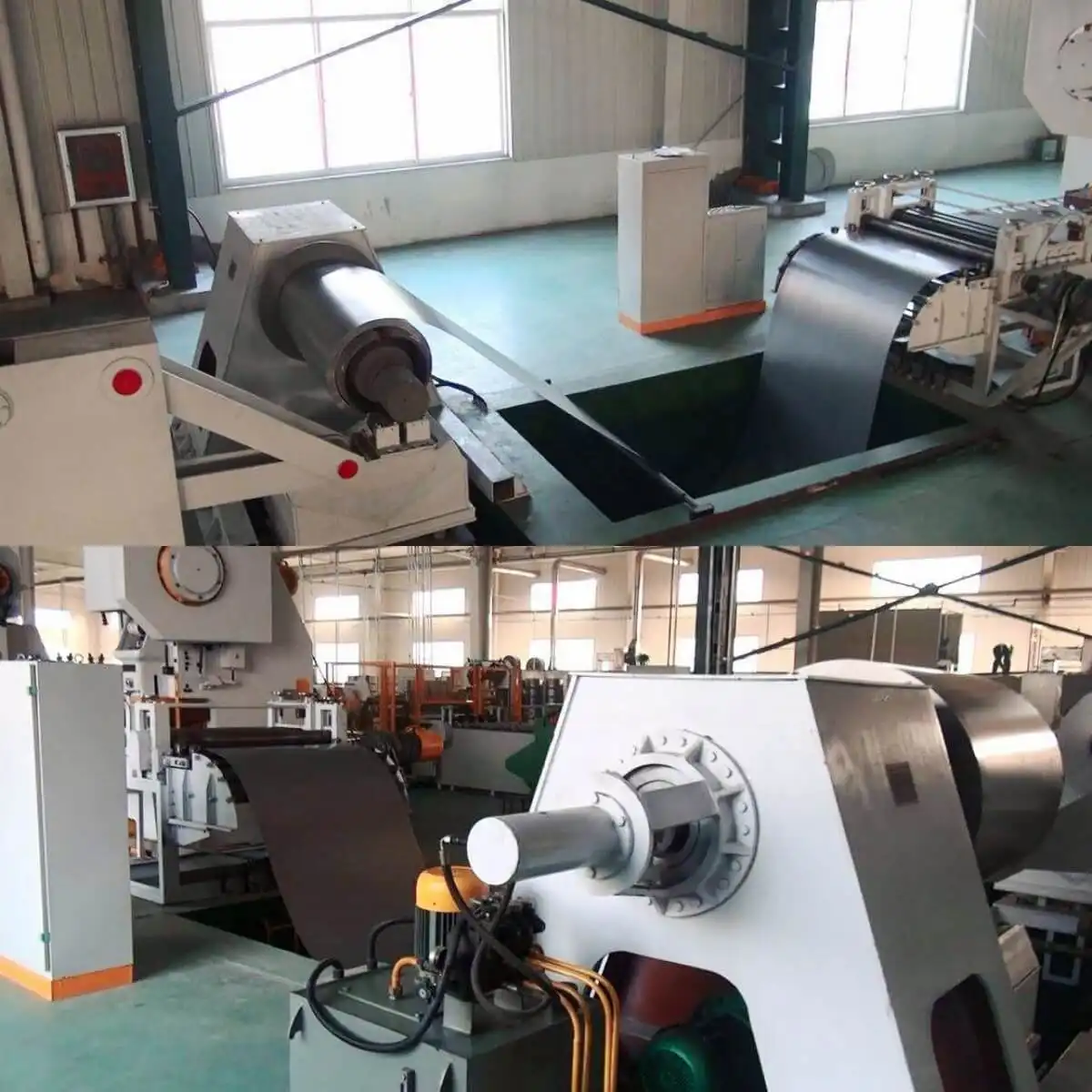
Decoiling Straightening & Shearing Machines
Decoiling Machine:
- Sheet Width: 600-1320mm
- Thickness: 0.6-1.4mm
- Production Capacity: 15 cuts/min
- Max Cutting Speed: 50-60m/min
Seven Roller-Sizing Straightening Machine:
- Straightening Precision: ≤1.5mm/m²
Shearing Machine:
- Shearing Thickness: ≤3mm
- Shearing Width: ≤1500mm
Cover Pressing Machine
Cover Pressing Machine (160 Ton Press)
- Function: Forms the cover and bottom using two 160 Ton punch presses.
Double Locking Pressing Machine(63 Ton Press)
- Function: Used for normal drum hole punching and locking.
Automation: Loading and unloading are fully automated.
Unit Power: 15KW
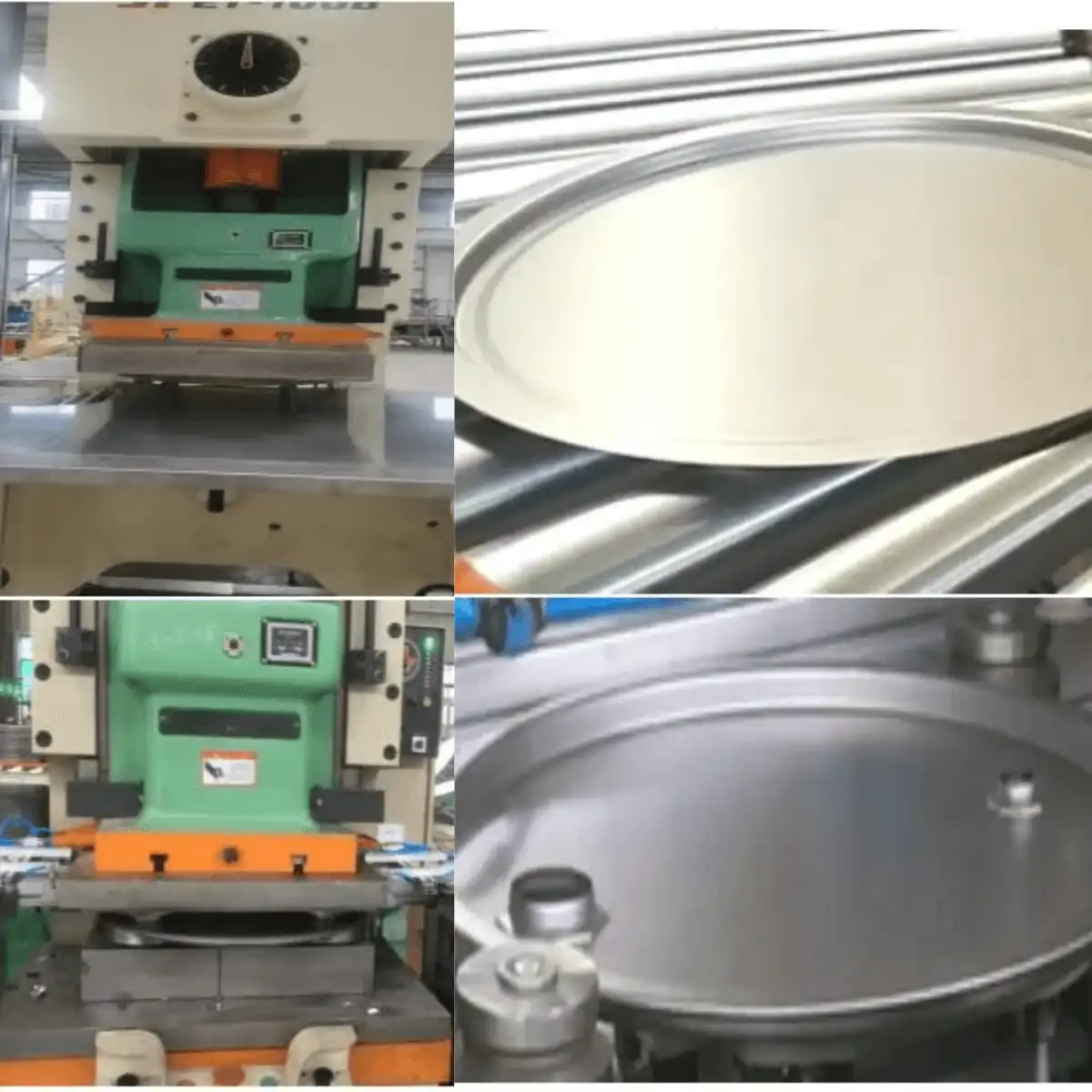
Pre Curling & Spray Sealing Glue Machine
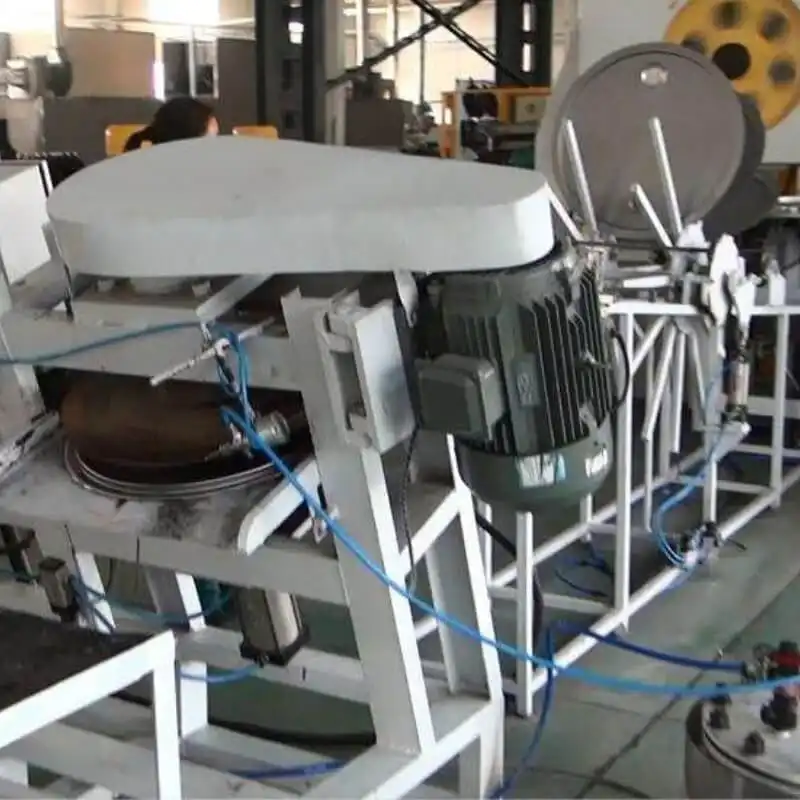
Automatic Palletizing Machine
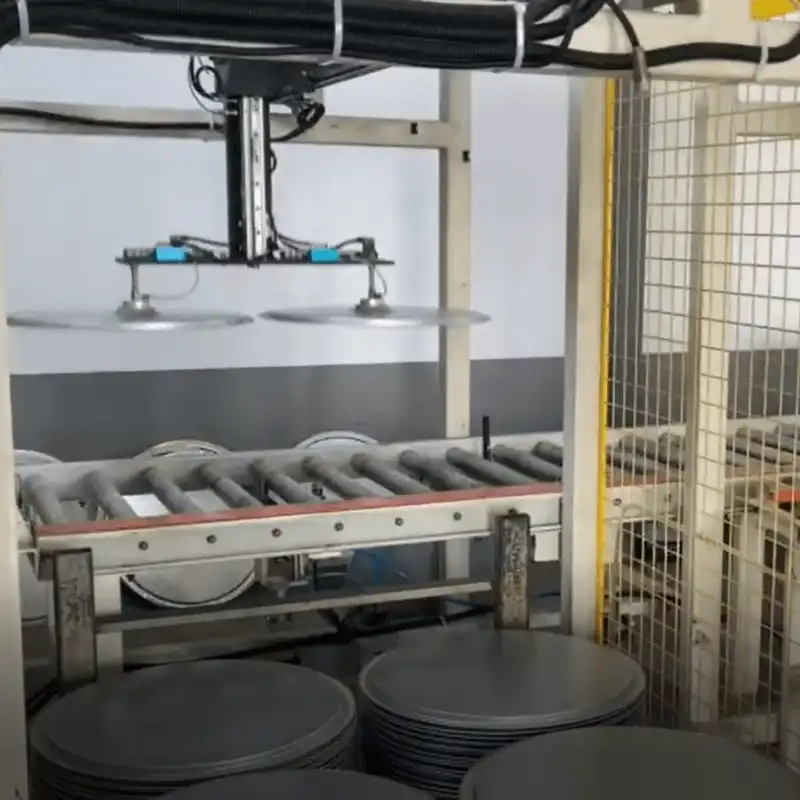
Spray painting Machines
Washing line
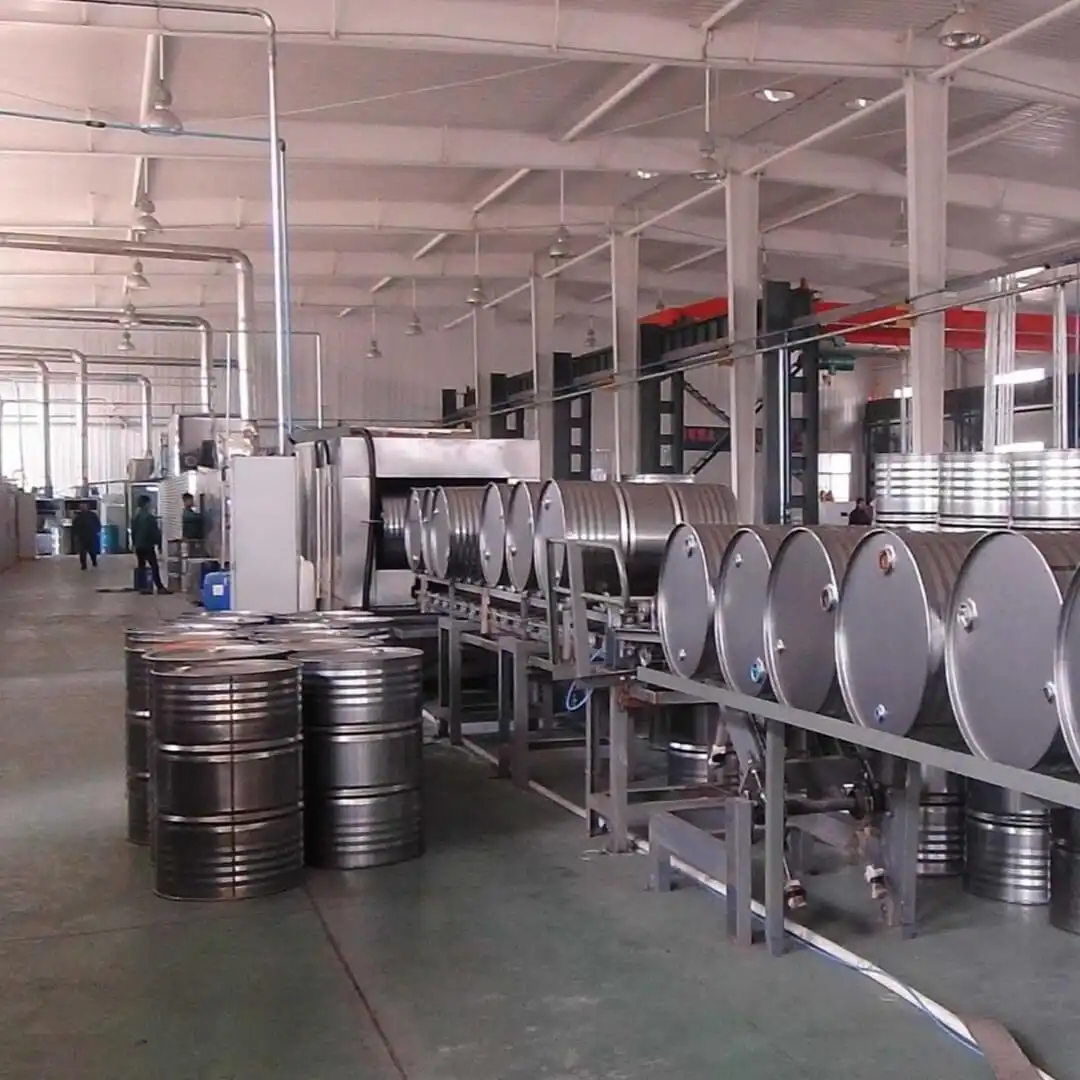
- Drums are cleaned and placed on the painting transport chain, transitioning from horizontal to vertical.
- Wash transportation Length:55 m
- Drying channel: L28m;W1.5m; H1.7m
Painting equipment
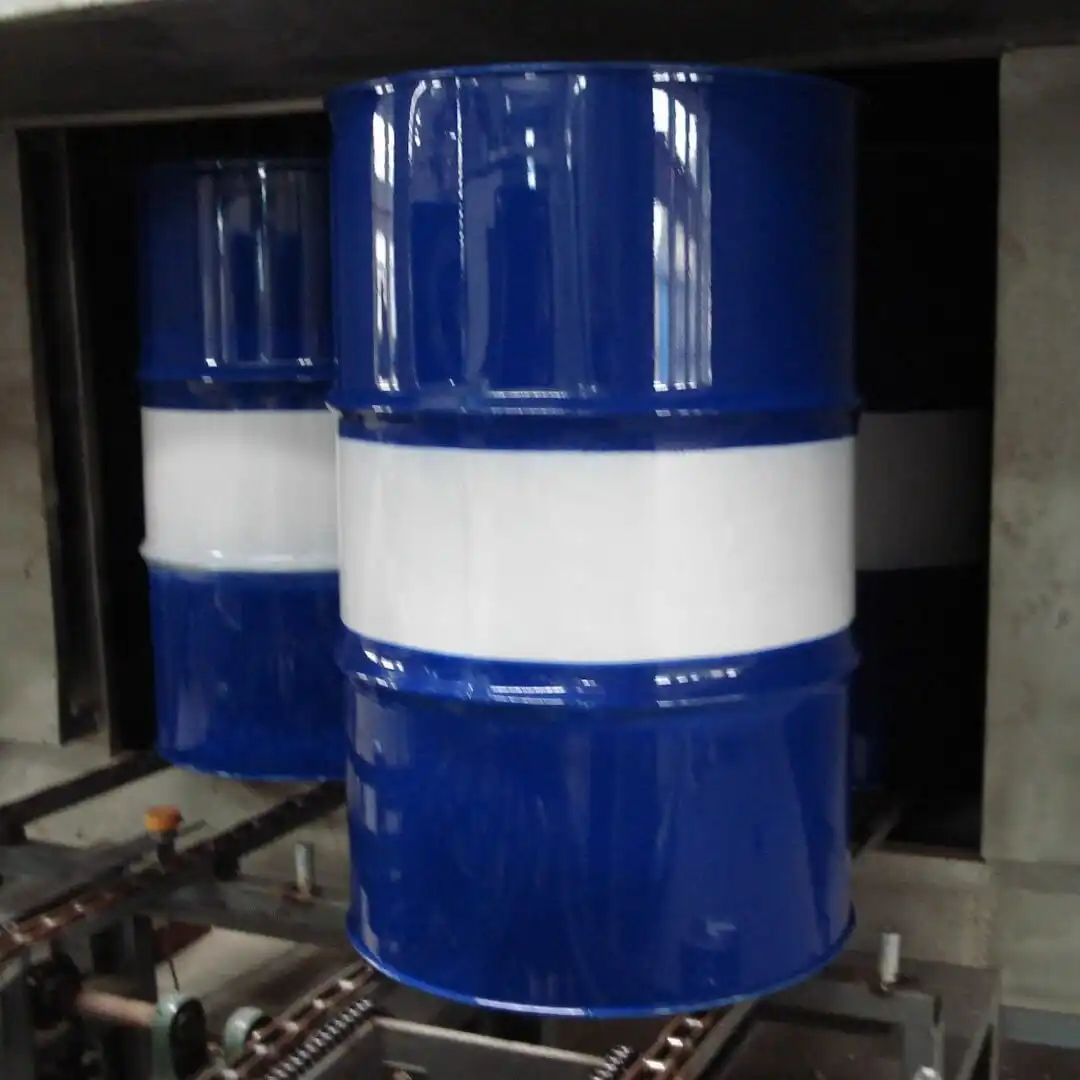
Three-color painting:
Inner: Waterproof paint
Outer: Acid alcohol magnetic paint
Size: L4.8m; W4m; H2.4m
Drying equipment

3-row vertical drying
Temperature control range: room temperature to 200°C, adjustable
Temperature control accuracy: ±5°C
Size: L36M; W2.6M; H2.1M
Cooling equipment
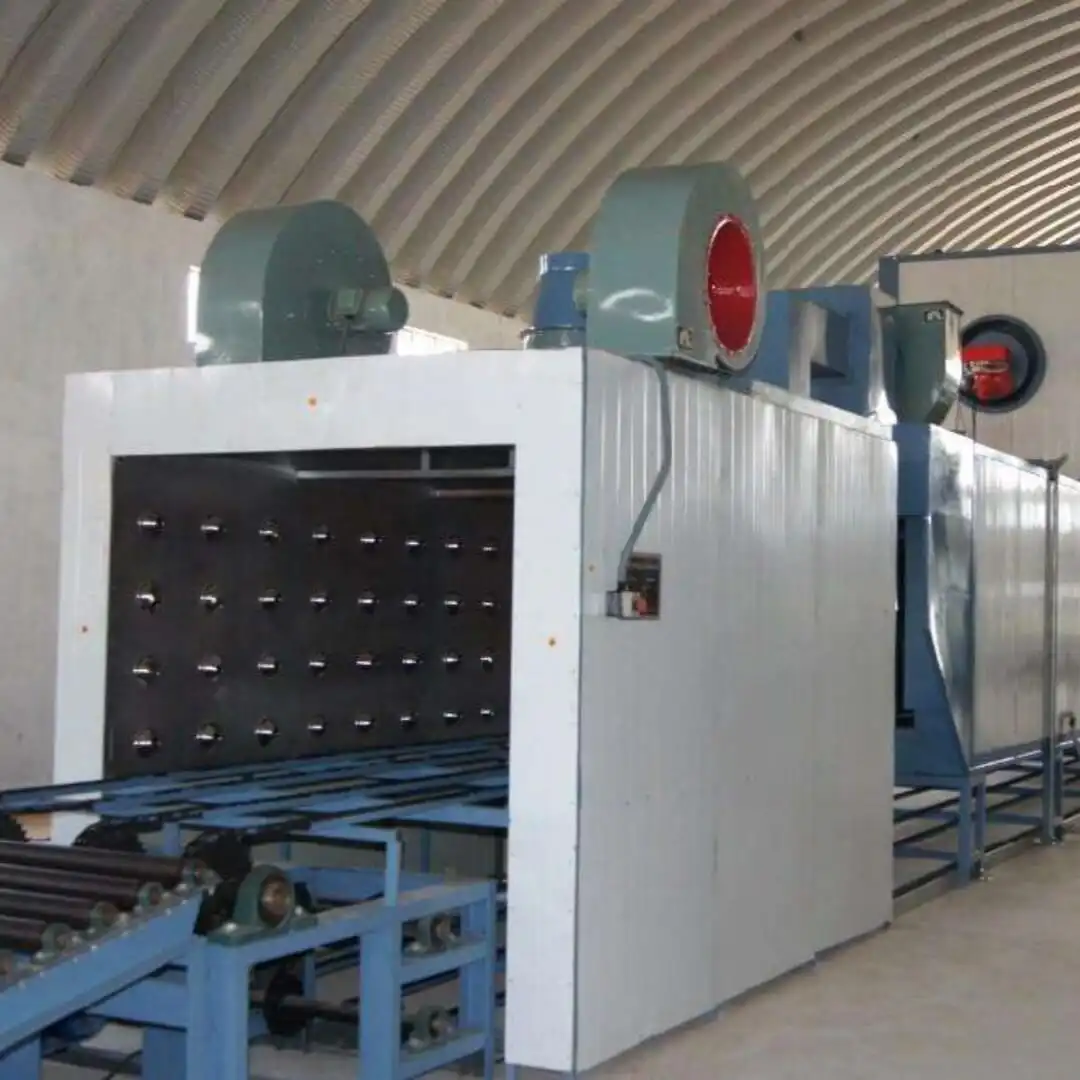
Function: Harden lacquer surface after baking
Power: 6.6 kW
Leakage test Machines
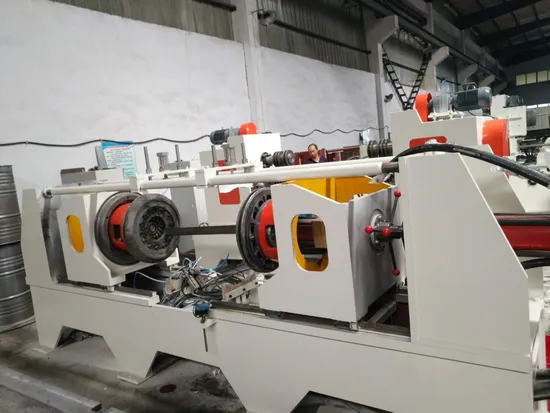
Leakage test Machines
Horizontal type test, air press 0.03Mpa.Controlled by PLC, compressed air driving.
Other informations
Product Details
Steel Drum Production Line Layout Diagram
Production Results
Welding Method:
This equipment uses a roll seam welding method, with electrodes in the form of cylindrical rollers. The width of the electrode is greater than the overlapping section of the steel plate, allowing control over the thickness of the joint. During the welding process, a higher electrode pressure and continuous welding current are applied. By controlling welding parameters such as electrode pressure, welding current, and welding time, stable welding quality can be achieved. The machine is capable of performing the seam welding process on longitudinal seams of metal drums with diameters ranging from 516mm (for conical drums) to 571.5mm.
Equipment Configuration List
Drum Ends Production Line | |||||
SN. | Model No. | Name | Unit | Quantity | Note |
1 | ST2311.00B | Up-Coil cart | set | 1 | Hydraulic drive |
2 | STK2010.01.00C | Uncoiling Unit | Set | 1 | Hydraulic drive;frequency control of motor speed |
3 | STK1213100 | 9 rollers leveler and Measurement facility | Set | 1 | servo control |
4 | ST1319.00 | Conveyer from leveler to press machine\ Scrap Sheet-cutting Machine | Set | 1 | |
5 | JD21-160 | Cover Pressing Machine | Set | 2 | 160 Ton |
6 | MJ571.5 | Mold for cover and bottom | Set | 2 | |
7 | ST1318.00 | Conveyer for cover to pre-coil and spry glue machine | Set | 2 | Include conveyer and stacking |
8 | YJX200900 | pre-coil and spry glue machine | Set | 2 | PLC control; |
9 | St-1001 | Auto stacking for drum lids | Set | 2 | |
10 | Q11-2000 | Scrap Sheet-cutting Machine | Set | 1 | 3*2000mm |
11 | KJKZ2011.00 | Electric control box | Set | 1 | |
12 | KJ2011.02.00 | Hydraulic station | Set | 1 |
Automatic punching 2′& 3/4′ hole and locking 2′& 3/4′ Closure | |||
SN. | Name | Unit | Quantity |
1 | Deep throat power 63 Ton press | Set | 2 |
2 | Double Pressing mold | Set | 1 |
3 | Double Locking mold | Set | 1 |
4 | Auto transport line for cover | Set | 1 |
5 | Electric control system | Set | 1 |
Cut to Length Line (for drum body) | |||||
SN. | Model No. | Name | Unit | Quantity | Note |
1 | ST2311.00B | Up-Coil cart | set | 1 | Hydraulic drive |
2 | STK2010.01.00C | Uncoil Unite | Set | 1 | Hydraulic drive |
3 | STK1213100 | 9 rollers leveler machine | Set | 1 | Frequency adjust speed |
4 | STK1213200 | Measurement facility | Set | 1 | servo motor |
5 | Q11-1500 | Sheet-Cutting Machine | Set | 1 | 3*1500mm |
6 | KJKZ2011 | Electric control box | Set | 1 | |
7 | KJ2011.02.00 | Hydraulic station | Set | 1 |
Steel Drum Body Production Line | |||||
SN. | Model No. | Name | Unit | Quantity | Note |
1 | KJJQ.00 | Conveyer | Cutting line | ||
2 | FHJ-250-2 | Auto-welder machine | Set | 1 | Three-phase medium frequency inverter |
3 | YP-line201 | Welding line rolling compaction and Cut out the tongue of iron | Set | 2 | |
4 | STG2201.00 | Extrusion flange machine | Set | 1 | Includes Multi working-step Chain and electric control hydraulic control |
5 | STG2203.00 | Beading machine | Set | 1 | Includes Multi working-step Chain and electric control hydraulic control |
6 | STG2202. 00 | Corrugating machine | Set | 1 | Includes Multi working-step Chain and electric control hydraulic control |
7 | STG1005.00 | welding line Leakage test machine | Set | 1 | Includes Multi working-step Chain and electric control hydraulic control |
8 | ST2204.05.00 | Auto feeding for drum ends | Set | 1 | Includes Multi working-step Chain and electric control |
9 | ST2204.00X | Seaming machine | Set | 1 | Includes Multi working-step Chain and electric control hydraulic control |
10 | STG1005.00 | Leakage test machine | Set | 1 |
Rear Treatment (Wash, Drying, Painting System, Etc.) | ||||
SN. | Name | Unit | Quantity | Note |
1 | Lift machine | Set | 1 | |
2 | Washing, cleaning and transport | Set | 1 | |
3 | Drying and transport | Set | 1 | |
4 | Turning machine | set | 2 | |
5 | Painting room(outside) | set | 2 | 3 colors |
6 | Front distributor | Set | 2 | |
7 | Vertical three channel drying equipment | Set | 1 | (outside) |
8 | Cooling | Set | 1 | |
9 | Rear distributor | Set | 1 |
Technical Services
Adhere to customer-centricity and provide your company with comprehensive pre- sales and after-sales services such as installation, commissioning, training, and maintenance.
Pre-sales service: Before signing the contract, the company provides customers with various production process solutions and technical consulting services for equipment.
Installation and commissioning: According to the contract, our company will safely transport the equipment to the installation site designated by the user within the specified time, and send technical service engineers to install it on site. When the user has the basic installation and commissioning spare parts, the technical service engineer will install and debug the machine for the user to use, ensuring that the installation and commissioning site environment is neat, clean and orderly.
After-sales Training: The company offers free technical training (min. 5 days) at the buyer’s site or the seller’s training center. Key topics include:
- -Control software usage
- -Power on/off procedures
- -Panel and software parameter settings
- -Basic machine cleaning and maintenance
- -Handling common hardware failures
- -Operational precautions
Equipment maintenance
- -One-year warranty after final acceptance;
- -Customer service response time is within 24 hours;
- -Paid repairs are provided after the warranty period.